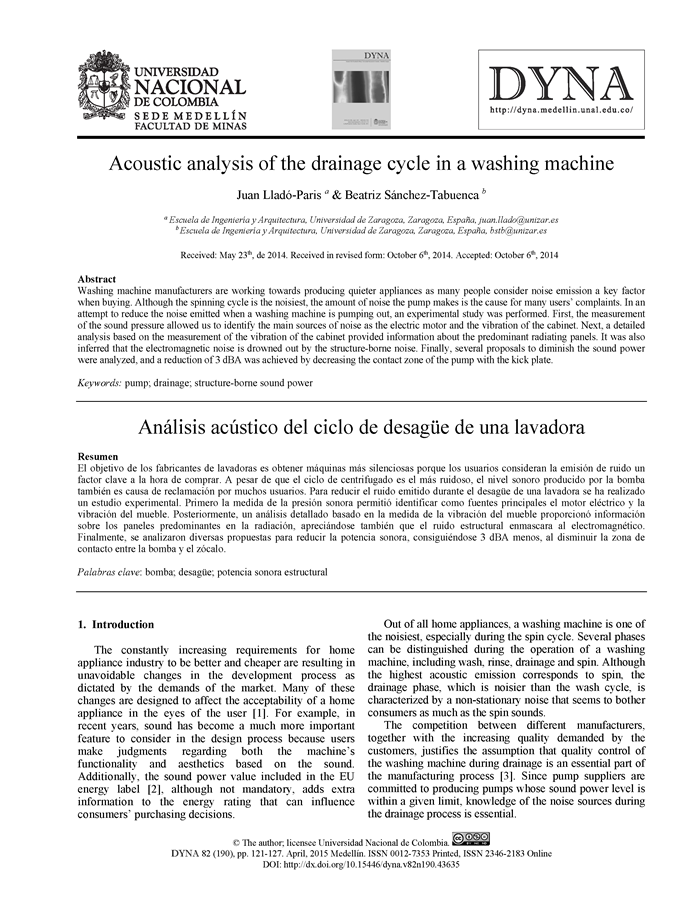
Publicado
Acoustic analysis of the drainage cycle in a washing machine
DOI:
https://doi.org/10.15446/dyna.v82n190.43635Palabras clave:
pump, drainage, structure-borne sound power (es)
Descargas
DOI: https://doi.org/10.15446/dyna.v82n190.43635
Acoustic analysis of the drainage cycle in a washing machine
Análisis acústico del ciclo de desagüe de una lavadora
Juan Lladó-Paris a & Beatriz Sánchez-Tabuenca b
a Escuela de Ingeniería y Arquitectura, Universidad de Zaragoza,
Zaragoza, España, juan.llado@unizar.es
b Escuela de Ingeniería y Arquitectura, Universidad de Zaragoza,
Zaragoza, España, bstb@unizar.es
Received: May 23th, de 2014. Received in revised form: October 6th, 2014. Accepted: October 6th, 2014
This work is licensed under a Creative Commons Attribution-NonCommercial-NoDerivatives 4.0 International License.
Abstract
Washing machine
manufacturers are working towards producing quieter appliances as many people
consider noise emission a key factor when buying. Although the spinning cycle
is the noisiest, the amount of noise the pump makes is the cause for many
users' complaints. In an attempt to reduce the noise emitted when a washing
machine is pumping out, an experimental study was performed. First, the
measurement of the sound pressure allowed us to identify the main sources of
noise as the electric motor and the vibration of the cabinet. Next, a detailed
analysis based on the measurement of the vibration of the cabinet provided
information about the predominant radiating panels. It was also inferred that
the electromagnetic noise is drowned out by the structure-borne noise. Finally,
several proposals to diminish the sound power were analyzed, and a reduction of
3 dBA was achieved by decreasing the contact zone of the pump with the kick
plate.
Keywords: pump; drainage; structure-borne sound power
Resumen
El objetivo
de los fabricantes de lavadoras es obtener máquinas más silenciosas porque los
usuarios consideran la emisión de ruido un factor clave a la hora de comprar. A
pesar de que el ciclo de centrifugado es el más ruidoso, el nivel sonoro
producido por la bomba también es causa de reclamación por muchos usuarios.
Para reducir el ruido emitido durante el desagüe de una lavadora se ha
realizado un estudio experimental. Primero la medida de la presión sonora
permitió identificar como fuentes principales el motor eléctrico y la vibración
del mueble. Posteriormente, un análisis detallado basado en la medida de la
vibración del mueble proporcionó información sobre los paneles predominantes en
la radiación, apreciándose también que el ruido estructural enmascara al
electromagnético. Finalmente, se analizaron diversas propuestas para reducir la
potencia sonora, consiguiéndose 3 dBA menos, al disminuir la zona de contacto
entre la bomba y el zócalo.
Palabras clave: bomba; desagüe; potencia sonora estructural
1. Introduction
The constantly increasing requirements for home appliance industry to be better and cheaper are resulting in unavoidable changes in the development process as dictated by the demands of the market. Many of these changes are designed to affect the acceptability of a home appliance in the eyes of the user [1]. For example, in recent years, sound has become a much more important feature to consider in the design process because users make judgments regarding both the machine's functionality and aesthetics based on the sound. Additionally, the sound power value included in the EU energy label [2], although not mandatory, adds extra information to the energy rating that can influence consumers' purchasing decisions.
Out of all home appliances, a washing machine is one of the noisiest, especially during the spin cycle. Several phases can be distinguished during the operation of a washing machine, including wash, rinse, drainage and spin. Although the highest acoustic emission corresponds to spin, the drainage phase, which is noisier than the wash cycle, is characterized by a non-stationary noise that seems to bother consumers as much as the spin sounds.
The competition between different manufacturers, together with the increasing quality demanded by the customers, justifies the assumption that quality control of the washing machine during drainage is an essential part of the manufacturing process [3]. Since pump suppliers are committed to producing pumps whose sound power level is within a given limit, knowledge of the noise sources during the drainage process is essential.
The main element of the drainage system is a synchronous pump that is installed and enclosed in a washing machine. It consists of a permanent magnetic electric motor running at the mains voltage and a plastic housing unit containing a centrifugal impeller working on a common shaft (Fig.1). The pump sucks water from the bottom of the wash tub through the inlet hose and when water enters the pump, the impeller creates the vortex required to force it out through the drain hose to the waste water pipe. The pump is fastened to the kick plate of the washing machine with a screw and a lid (Fig. 2).
During the operation of the pump, vibrations are transmitted to the cabinet through their common fastening. It is important to take this into account since some authors [4, 5] pay special attention to the structure-borne noise of home appliances, which is mainly caused by the vibration of the cabinet.
Although a great number of washing machines are manufactured each year, detailed studies of the noise sources during the drainage of a washing machine have not yet been found in the available literature. Only Park et al. [6] stated that one of the main failures of a washing machine's drain pump is noise. However, they focused on an accelerated test to evaluate the reliability of the pump assembly without analyzing the possible noise sources.
Consequently, there is a need for an improved understanding of the general noise and vibration characteristics of drain pumps in order to develop quieter washing machines. To reduce the noise produced by pump operation, it is necessary to rate the noise produced by the pump itself as well as the acoustic radiation from the vibrating cabinet during the drainage cycle. This analysis will deliver insight into which changes to the pump can be performed and tested to prove their effectiveness. For this reason, an experimental approach was performed to calculate the sound power during drainage and to obtain the structural noise based on measurements of surface vibration.
The procedure is summarized as follows:
(1) Analysis of the evolution of the sound pressure during drainage to determine which acoustic pressure interval is the most relevant and must be considered on all tests carried out. Set up of the experimental study to calculate the sound power during this phase drainage, based on ISO 3744 [7]. (2) Identification of the potential noise sources and experimental determination of the structural sound power for different fastening conditions between the cabinet and the pump in order to rate the noise sources. The velocity vibration distributions will provide guidance for design modifications. (3) Proposal of design modifications of the pump system and evaluation of their effectiveness.
2. Acoustic investigation of the drainage phase
2.1. Noise measurement setup
During drainage, different noises can be perceived depending on the conditions of the process. Therefore, the condition of drainage during which noise measurements will be performed has to be selected. To define which state of the drainage phase is the most significant, an A-weighted sound pressure level (Fig. 3) was recorded with a microphone placed in front of the washing machine, at a horizontal distance of 1 m and a height of 1 m.
Following this analysis, the three following phases were observed: (1) when only water is pumped, (2) when the pump is working at full load; and (3) following the peak that indicates the transition to the partial load when air and water are pumped. The highest acoustic level was obtained at the peak, but due to the peak level's variability and short duration, the partial load phase, which lasts longer, was chosen as the state of drainage to analyze.
Once the measurement phase was established, the sound power was chosen as the parameter used to objectively quantify the noise emissions of the different tests. Sound power is a measure of the amount of sound energy a noise source produces per unit time, independent of its surroundings. It is an important absolute parameter that is widely used for rating and comparing sound sources. Calculation of this value was based on sound pressure measurements as applied to home appliances according to the specifications of ISO 3744. Measurements were performed in a semianechoic room with a reflecting wall and floor. The washing machine was located against the reflecting wall for normal usage. A parallelepiped reference box enclosing the washing machine was delineated to define the measurement surface's dimensions, where the A-weighted sound pressure level was measured, during a 20 s interval, by six microphones 4189 B&K, that surrounded the washing machine at different positions as specified by ISO 3744. A B&K Pulse multianalyzer was also used. In addition to sound pressure time records, FFT spectra were also computed to find out the noise contribution of different sources within drainage. The frequency range of the FFT spectra extended from 0 Hz to 3,2 KHz as values above this limit were considered negligible. Thirty pumps were used in the different tests carried out.
2.2. Noise sources
For most acoustic sources, the sound emission is a consequence of complex internal mechanisms which force machine parts to vibrate, causing the vibrations to radiate into the ambient air (airborne sound); pass through liquid-filled systems such as pipes (fluid-borne sound); or re-excite connected and supporting structures (structure-borne sound) [8]. Concerning the pump of a washing machine, the noise flow diagram depicted in Fig. 4 was developed to illustrate the noise generation and transmission process within the pump unit.
Noise and vibrations are generated within the electric motor, the impeller, and the water-air pulsations through the system. The motor vibrations and the water-air impulsion are transmitted to the pump housing and inlet/drain hoses, and may be radiated from the housing as airborne noise or retransmitted as vibration from the housing to the cabinet via the pump fixation or the hose attachments. Other noise sources include electromagnetic motor noise produced by the magnetic forces generated in the gap between the rotor and stator and fluid-borne noise provoked by randomly excited forces caused by interaction of the turbulent flow, the impeller and the drain hose. Mechanical noise due to the bearings and any imbalances of the rotor are considered less important because the system is well lubricated and balanced.
2.3. Experimental evaluation
In order to evaluate the noise transmitted through each path, several tests examining the way the pumping system is fastened to the cabinet were performed. The first test was undertaken to determine the sound power during drainage at standard conditions. The objective of the second and third tests was to understand the influence of the vibrations induced by the drain hose and the pump housing. The drain hose and then the pump were unfastened from the cabinet in the second and third tests, respectively. For each case, Table 1 shows the sound power obtained out of an average of 40 tests in order to reduce the influence of random noise. The sound power level obtained at standard conditions did not differ from the case when the drain hose was not attached to the cabinet; therefore, the vibrations of the cabinet due to the water-air impulsion through the drain hose were negligible.
However, when the pump was not fixed to the cabinet, the sound power decreased by about 9 dBA. In order to identify the main noise sources of each case, standard operation and unfastened pump, the narrowband spectra between 0 and 3200Hz was recorded with a microphone in front of the washing machine, placed at position 1 according to ISO 3744, and shown in Fig. 5.
All noise generating mechanisms combined to produce a noise spectrum characterized by broadband noise with pronounced discrete frequency tones. At standard operation, the total emitted noise was generated partially by the cabinet and partially by the electric motor and consisted of structural and electromagnetic noise origins. The broadband noise was produced by the vibration of the cabinet (generated by the pump) and the discrete frequency tones were mainly created by the electric motor at multiples of twice the drive frequency [9]. When the pump was not fastened to the cabinet, the broadband noise was practically reduced to below 10 dBA and discrete frequency tones were maintained.
In order to know the relevance of both noise origins, a detailed analysis of the noise radiated by the cabinet was performed to obtain the structure-borne sound power and information about the predominant radiating panels of the cabinet.
2.4. Experimental evaluation
The characterization was based on the application of the ISO/TR 7849 standard [10]. This is an experimental approach to calculate the structure-borne sound power level LWS of a structure eq. (1) from the mean vibratory velocity level, the reference velocity being vo = 5.10-8 m/s.
Where, the mathematical symbols of and
denote mean vibratory velocity level, area of
the radiating structure, area of reference equal to 1 m2, radiation
factor [11], impedance of the air, and impedance of the air at 20°C and
atmospheric pressure of 105 Pa, respectively. The value of the mean
vibratory velocity level was obtained by measuring the normal vibratory
velocity at n points of each radiating surface considered, and the radiation
factor was calculated according to eq. (2):
Where, P and A are the perimeter
and area of the surface, respectively; K=0.3h, h being the thickness of theplate; being the velocity of
the waves in a plate, with E, the elastic modulus and rM, the main density of the material; c, the sound velocity; f, the wave frequency; and
, the critical frequency of a plate.
2.4.1. Calculation of the mean vibratory velocity level
The cabinet of the washing machine was subdivided into the following five radiating surfaces: the two side panels, the rear panel, the front plate and the kick plate where the pump is linked. Each panel was divided into a number of areas having similar geometric and transverse vibratory response characteristics.
The right, left and rear panels were divided into twelve parts of equal area. According to their natural boundaries, the front and kick plates were partitioned in six and four areas, respectively, defining its center position for vibration measurement. For example, Fig. 6 shows the six measurement points at the front plate.
The measurement of the vibratory velocity using Deltatron 4397 B&K accelerometers and a B&K Pulse multianalyzer was performed, at any of the defined points, during standard operation and when the pump was not attached to the kick plate. Measurements were repeated five times for each case. As an example, Fig. 7 shows the FFT spectra of the vibratory velocity at the six points of the front plate during standard operation. The behavior of all points is similar, but the vibration level decreases as the measurement points are farther from the pump, with a difference of 4 dBA between the maximum level, at point 2, and minimum level at point 6.
For each plate, the mean vibratory velocity level, , was calculated from the vibration velocity
measured at each point, Lvi,
according to eq. (3). The right, left and rear panels were divided into N=12
parts of equal area, and the front and kick plates into N=6 and N=4 parts of
different area Si, respectively:
Fig. 8 shows the results for the standard operation and the unfastened pump. Maximum velocity values extended up to 400 Hz, as is also reflected in the noise spectra of Fig. 5. When the pump was not attached, the vibration velocity level dramatically decreased since the vibrations induced by the pump were not directly applied to the cabinet. The discrete frequency tones, multiples of 50 Hz, also appeared up to 600 Hz, as the motor aerodynamically excited the cabinet.
2.4.2. Numerical results and discussion
The average results of the structural sound power level, eq. (1), emitted by the cabinet panels of the five washing machines analyzed are shown in Table 2. During standard operation, the noisiest elements were the kick and front plates, followed by the left and right sides. The rear panel barely contributed to the noise. Additionally, it was demonstrated that the contribution of the kick plate to the structure-borne noise was great despite the fact that the kick plate is smaller than the other panels. When the pump was not fixed to the kick plate, this relationship was inverted because the pump was not directly connected to the cabinet and the contribution of the kick plate was not significant. The pump was attached to the tub of the oscillating group (Fig. 9) by the inlet hose and the cabinet was excited through the springs and shock absorbers closest to the side panels. Since the pump was not directly joined to any panel, the vibration transmitted was dampened through the oscillating group and the sound power level caused by structural radiation decreased 20 dBA. In this case, the main source was the electromagnetic noise as can be seen by the comparison of the total and structural sound power.
The subtraction of the sound power level-caused mainly by the motor-obtained when the pump was loosened (see Table 1), leaves 59 dBA that corresponded to the structure-borne noise of the cabinet which matched the results obtained for the structure-borne sound power (see Table 2).
At standard operating conditions, it was inferred from the tests that the total sound power was mainly structure- borne, as a result of the interaction between the pump and the cabinet. This depends on the design, mass, rigidity and damping of the washing machine elements and the vibration magnitude depends on the excitation force [12].
According to eq. (1), control of sound radiation from a vibrating structure can be achieved by reducing either the vibration level of the structure or the radiation ratio. This study, primarily focused on the pump system, eliminates the option of the radiation factor given that it is inherent to the cabinet. The control of the sound during drainage will be guided by the reduction of the vibration level of the cabinet. Following, several modifications of the pump system are analyzed.
3. Analysis of proposals for noise reduction
The modifications to the pump system must be capable of being put into practice in a short time to reduce the sound power without adding too much cost. As discussed in the preceding section, the force transmitted by the water pulsations and the electric motor vibrations to the cabinet through their common fastening is the main noise source, and the vibration magnitude of the cabinet depends on the level of this excitation force.
This can either be reduced directly at the source or the energy transmission path can be broken.
Flow in centrifugal pumps produces turbulence, unsteadiness, etc. [13]. The relative movement between the impeller and housing generates an unsteady interaction which affects not only the overall pump performance but is also responsible for pressure fluctuations that interact with the housing or circuit and give rise to unsteady forces over the mechanical parts [14]. These are the most important sources of vibration. Increasing the clearance between the impeller and the housing is a widely used method for noise control. The flow resistance can be reduced by broadening the flow channel. Changes in the geometry or configuration of the impeller or the housing such as a decrease in the diameter of the impeller, the number of blades and the blade width of the impeller broaden flow passage or channel, and lead to the reduction of flow resistance. However, pump performance and efficiency are normally adversely affected by such changes. Finding a good match between the impeller and pump housing to reduce the noise without decreasing efficiency requires an exhaustive analysis to understand the highly complex flow interactions that occur in the pump and control the fluctuating pressure field that gives rise to dynamic forces. These investigations are beyond the scope of this study.
The preferred method chosen to reduce the noise during drainage has been directed towards the transmission path. One option could be to use an elastic or transmission element at the interface between the pump and cabinet to effectively damp the level of the transmitted force. However, this becomes very expensive because the damping devices have to be applied to every single product. Another way to damp the excitation force is to reduce the contact pressure between the pump and the cabinet. This can be achieved by decreasing the thickness of the zone of the pump housing unit that is in contact with the cabinet.
The only cost is the modification of the die, and this solution can be quickly implemented. In the following section, the results of such a modification are presented.
3.1. Modification of the pump fastening
The pump housing area that is in contact with the kick plate is a ring area with a top lid, and a lower hole to screw the pump into the cabinet, as illustrated by Fig. 10.
The modification of this fastening zone includes reducing the thickness of the ring area by 0,6 mm to diminish the pressure between the pump and the kick plate.
Ten prototypes were manufactured, and the average sound power, calculated according to ISO 3744, was equal to 57 dBA. A reduction of the total sound power level of 3 dBA was achieved with this easy to implement solution that barely increases the production cost, because it only requires the modification of the mold of the housing. To analyze the influence of this change on the noise radiated by the cabinet, the structure-borne sound power was also computed. The kick and the front plates reduced the radiated sound power up to 4 dBA. However, this does not deal with the panels that contribute the most to the structure-borne noise.
As it was expected, the broadband noise produced by the vibration of the cabinet is reduced (See Fig 11), achieving a 3 dBA decrement of the total radiated sound power, as shown in Table 3.
4. Conclusions
Pump manufacturers have to face the ever stricter sound quality controls of home appliances companies. This means that the sound power levels during drainage must be within a specified limit. To easily meet this specification, the analysis of the noise sources during drainage was performed to control noise emission. During the operation of the pump, the total emitted noise was partially electromagnetic, generated by the motor, and partially structure-borne, due to the vibration of the cabinet induced by the pump. The analysis of the measurements and results showed that the radiated noise prevailed over the electromagnetic noise. This structure-borne noise cannot be controlled through the pump production process, but efforts have been made to reduce the interaction between the pump and cabinet of the home appliance. The reduction in the thickness of the pump-cabinet contact surface served to diminish the contact pressure between both elements, achieving a drop in the structure-borne sound power of 3 dBA.
At first, experiments were carried out to determine the noise sources during the drainage, and to analyze the contribution of each element toward the total noise emission. Further studies to reduce the noise emitted during drainage must consider design modifications on both the pump system and the cabinet. The modification of the pump should be aimed at minimizing the forces caused during its operation without decreasing its efficiency. Initially, the flow field should be studied to introduce the design modifications of the impeller and pump housing that decrease the flow resistance. To reduce structure-borne noise, the cabinet plates should be stiffened and the viability of the attachment of the pump to other areas, such as the base of the cabinet, to absorb the transmitted forces should be analyzed.
References
[1] Lyon, R.H., Designing for product sound quality. New York: Marcel Dekker, Inc., 2000.
[2] CEC (Council of the European Communities)., Council Directive 92/75/EEC of 22 September 1992 on the indication by labeling and standard product information of the consumption of energy and other resources by household appliances. Official Journal L 297, 1992, pp. 16-19.
[3] Mentes F. and Ozturk, C., Identification of the possible noise sources of the washing machine and further studies over the applicable noise reduction methods, Proceedings of Euro Noise '92, Books 1-3 (14), pp. 697-677, part 4, 1992.
[4] Vercammen, M.L.S. and Heringa, P.H., Characterising structure-borne sound from domestic appliances. Applied Acoustics, 28 (2), pp.105-117, 1989. https://doi.org/10.1016/0003-682X(89)90013-3
[5] Čudina, M. and Prezelj, J., Noise generation by vacuum cleaner suction units. Part III: Contribution of structure-borne noise to total sound pressure level. Applied Acoustics, 68 (5), pp.521-537, 2007. https://doi.org/10.1016/j.apacoust.2006.10.001
[6] Park S.J, Park S.D, Kim K.W., Cho J.H., Reliability evaluation for the pump assembly using an accelerated test. International Journal of Pressure Vessels and Piping, 83 (4), pp. 283-286, 2006. https://doi.org/10.1016/j.ijpvp.2006.02.014
[7] ISO 3744:1994. Acoustics- Determination of sound power levels of noise sources using sound pressure- Engineering method in an essentially free field over a reflecting plane. 1996.
[8] Hamilton, J.F., Measurement and control of compressor noise. West Lafayette, USA: Purdue University, 1988.
[9] Petersson B.A.T and Gibbs B.M., Towards a structure-borne sound source characterization. Applied Acoustics, 61 (3), pp. 325-343, 2000. https://doi.org/10.1016/S0003-682X(00)00037-2
[10] ISO/TR 7849:1987. Acoustics- Estimation of airborne noise emitted by machinery using vibration measurement, 2009.
[11] Fahy, F.J., Sound and structural vibration. 6th ed. London UK: Academic Press, 2000.
[12] Čudina, M. and Prezelj, J., Noise generation by vacuum cleaner suction units: Part I. Noise generating mechanisms - An overview. Applied Acoustics, 68 (5), pp.491-402, 2007. https://doi.org/10.1016/j.apacoust.2006.10.003
[13] Brennen, C.E., Hydrodynamics of pumps. Oxford University Press and CETI Inc.: Oxford, 1994.
[14] Adkins, D.R. and Brennen C.E., Analysis of hydrodynamic radial forces on centrifugal pump impellers. ASME J. Fluids Eng., 110 (1), pp. 20-28, 1998. https://doi.org/10.1115/1.3243504
J. Lladó-Paris, received the BSc. in Industrial Engineering in 1979, from the University of Barcelona, Spain, and the PhD. in Industrial Engineering in 1983, from the University of Zaragoza, Spain. In 1980, he joined the Department of Mechanical Engineering of the University of Zaragoza, being Associate professor since 1986. His research interests include dynamics and vibration of mechanical systems and design of plastic parts. He collaborates in the mechanical design of household appliances with several companies ORCID: 0000-0002-4367-3729
B. Sánchez-Tabuenca, obtained the BSc in Industrial Engineering in 1991 and the PhD in 1998 in Industrial Engineering all of them from the University of Zaragoza, Spain. In 1992, she joined the Department of Mechanical Engineering of the University of Zaragoza, where was promoted to Associate professor in 2001. She collaborates with household appliances companies, in the design of plastic parts and in the study of noise and dynamic behavior of several appliances. ORCID: 0000-0003-3909-5599
Cómo citar
IEEE
ACM
ACS
APA
ABNT
Chicago
Harvard
MLA
Turabian
Vancouver
Descargar cita
Licencia
Derechos de autor 2015 DYNA

Esta obra está bajo una licencia internacional Creative Commons Atribución-NoComercial-SinDerivadas 4.0.
El autor o autores de un artículo aceptado para publicación en cualquiera de las revistas editadas por la facultad de Minas cederán la totalidad de los derechos patrimoniales a la Universidad Nacional de Colombia de manera gratuita, dentro de los cuáles se incluyen: el derecho a editar, publicar, reproducir y distribuir tanto en medios impresos como digitales, además de incluir en artículo en índices internacionales y/o bases de datos, de igual manera, se faculta a la editorial para utilizar las imágenes, tablas y/o cualquier material gráfico presentado en el artículo para el diseño de carátulas o posters de la misma revista.