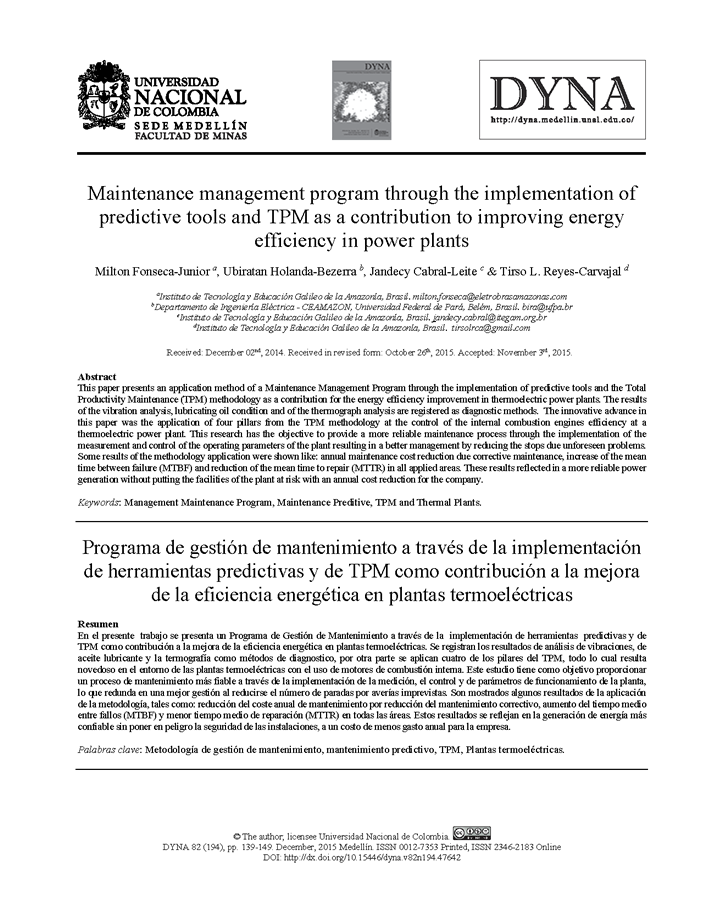
Publicado
Maintenance management program through the implementation of predictive tools and TPM as a contribution to improving energy efficiency in power plants
DOI:
https://doi.org/10.15446/dyna.v82n194.47642Palabras clave:
Management Maintenance Program, Maintenance Preditive, TPM and Thermal Plants. (es)DOI: https://doi.org/10.15446/dyna.v82n194.47642
Maintenance management program through the implementation of predictive tools and TPM as a contribution to improving energy efficiency in power plants
Programa de gestión de mantenimiento a través de la implementación de herramientas predictivas y de TPM como contribución a la mejora de la eficiencia energética en plantas termoeléctricas
Milton Fonseca-Junior a, Ubiratan Holanda-Bezerra b, Jandecy Cabral-Leite c & Tirso L. Reyes-Carvajal d
a Instituto de Tecnología y Educación Galileo de la Amazonía,
Brasil. milton.fonseca@eletrobrasamazonas.com
b Departamento de Ingeniería Eléctrica - CEAMAZON, Universidad
Federal de Pará, Belém, Brasil. bira@ufpa.br
c Instituto de Tecnología y Educación Galileo de la Amazonía,
Brasil. jandecy.cabral@itegam.org.br
d Instituto de Tecnología y Educación Galileo de la Amazonía,
Brasil. tirsolrca@gmail.com
Received: December 02nd, 2014. Received in revised form: October 26th, 2015. Accepted: November 3rd, 2015.
This work is licensed under a Creative Commons Attribution-NonCommercial-NoDerivatives 4.0 International License.
Abstract
This paper presents an application method of a Maintenance Management
Program through the implementation of predictive tools and the Total
Productivity Maintenance (TPM) methodology as a contribution for the energy
efficiency improvement in thermoelectric power plants. The results of the
vibration analysis, lubricating oil condition and of the thermograph analysis
are registered as diagnostic methods. The innovative advance in this paper was the application of four pillars
from the TPM methodology at the control of the internal combustion engines
efficiency at a thermoelectric power plant. This research has the objective to
provide a more reliable maintenance process through the implementation of the
measurement and control of the operating parameters of the plant resulting in a
better management by reducing the stops due unforeseen problems. Some results
of the methodology application were shown like: annual maintenance cost
reduction due corrective maintenance, increase of the mean time between failure
(MTBF) and reduction of the mean time to repair (MTTR) in all applied areas.
These results reflected in a more reliable power generation without putting the
facilities of the plant at risk with an annual cost reduction for the company.
Keywords: Management Maintenance Program, Maintenance Preditive, TPM and Thermal Plants.
Resumen
En el presente trabajo se presenta un Programa de Gestión de Mantenimiento a través de
la implementación de herramientas predictivas y de TPM como contribución a la
mejora de la eficiencia energética en plantas termoeléctricas. Se registran los
resultados de análisis de vibraciones, de aceite lubricante y la termografía
como métodos de diagnostico, por otra parte se aplican cuatro de los pilares
del TPM, todo lo cual resulta novedoso en el entorno de las plantas
termoeléctricas con el uso de motores de combustión interna. Este estudio tiene
como objetivo proporcionar un proceso de mantenimiento más fiable a través de
la implementación de la medición, el control y de parámetros de funcionamiento
de la planta, lo que redunda en una mejor gestión al reducirse el número de
paradas por averías imprevistas. Son mostrados algunos resultados de la
aplicación de la metodología, tales como: reducción del coste anual de
mantenimiento por reducción del mantenimiento correctivo, aumento del tiempo medio
entre fallos (MTBF) y menor tiempo medio de reparación (MTTR) en todas las
áreas. Estos resultados se reflejan en la generación de energía más confiable
sin poner en peligro la seguridad de las instalaciones, a un costo de menos
gasto anual para la empresa.
Palabras clave: Metodología de gestión de mantenimiento, mantenimiento predictivo, TPM, Plantas termoeléctricas.
1. Introducción
En el presenta trabajo se incluye, la propuesta de implementación de técnicas de mantenimiento predictivo, (análisis de vibraciones, análisis del aceite lubricante en el monitoreo y control de las fallas y la implementación de cuatro pilares básicos del TPM teniendo como objetivo el incremento de la eficiencia energética
Los esquemas de reposición más antiguos son por edad del componente o instalación y política de sustitución en masa [1,2]. En el primer caso un componente es sustituido después de un determinado tiempo de explotación o cuando el mismo falla, lo que generalmente ocurre primero. En el segundo caso, todos los dispositivos de una determinada clase son sustituidos en determinados intervalos o cuando estos fallan.
Lo antes expuesto resulta en una mejor administración, pues el tiempo de explotación de los equipos generalmente no es conocido y resulta más económico que una política basada en la sustitución individual. Esquemas de sustitución más recientes en muchos casos están basados en modelos probabilísticos (por ejemplo, [3,4] lo que si bien puede aportar buenos resultados requiere del historial de las instalaciones y equipos lo que puede resultar bastante complejo en mucho de los casos. En la mayoría de los casos en las concesionarias de energía eléctrica a pesar de estar presenta la actividad de mantenimiento no goza de buena efectividad. A su vez, el concepto de la simplicidad en una empresa está asociada generalmente con procesos y soluciones de tecnología, cuyas características y procedimientos son estrictamente necesarios para satisfacer las necesidades especificas de requisitos que son fáciles de implementar, mantener y utilizar [5].
Para una evaluación completa de los efectos de una política de mantenimiento se tiene que saber cómo su aplicación extendería la vida útil de un componente medido en, por ejemplo, el tiempo medio hasta el fallo o entre fallos. Para descubrir eso, es necesario un modelo matemático del proceso de deterioro de los componentes que describa los efectos del mantenimiento. En los últimos diez años o más han sido propuestos varios de esos modelos [6,7].
La situación es bien diferente para los procesos de deterioro, donde algunas veces la nueva condición de fallo no es exponencialmente distribuida igualmente los tiempos entre etapas sucesivas de deterioro [8]. En un proceso de este tipo la función de riesgo aumenta y el mantenimiento traerá mejorías independientes de los tipos de distribución entre las etapas sucesivas [9].
Es así, que algún tipo de monitoreo (por ejemplo, la inspección) debe ser parte del modelo [10]. Otras características deseables se enumeran en el estudio de la siguiente manera. Identificación del sistema y la lista de componentes críticos y sus funciones.
Modo de falla y análisis de efectos y criticidad para cada componente seleccionado, la determinación del historial de fallos y el cálculo del tiempo medio entre fallos, categorización de los efectos de la falla (utilizando flujogramas apropiados) y determinación de posibles tareas de mantenimiento [11-13], la atribución de tareas de mantenimiento y la evaluación del programa, incluyendo el análisis de costos. [14].
PREMO - Optimización del Mantenimiento Preventivo, se basa en un amplio análisis de las tareas, en lugar del análisis de sistemas, con una capacidad para reducir drásticamente el número tareas de mantenimiento en una planta [15-17]. Programas como PREMO han sido muy útiles para garantizar la operación económica de centrales eléctricas. Sin embargo estos programas no ofrecen todos los beneficios y flexibilidad de los programas en basa a modelos matemáticos [18].
En otros enfoques desarrollados; de ellos, al menos dos están interesados en las aplicaciones de sistemas de potencia [19,20]. En [19], un modelo de mantenimiento que se deriva de ramas paralelas de componentes en serie, como frecuentemente encontramos en subestaciones, en [20], el mantenimiento y la confiabilidad de los dispositivos en espera son estudiados. Ambos son, en esencia, los modelos de sustitución, donde la reparación y mantenimiento son asumidos "como nuevas" condiciones.
Una planta de energía térmica consiste en conjunto de sistemas mecánicos y eléctricos que requieren una vigilancia constante para la producción de energía. Se necesitan los datos obtenidos a través de las acciones de monitoreo en la evaluación de la operación, el mantenimiento y el rendimiento de las plantas. Para este propósito, se utilizan las llamados Distributed Control Systems- DCS.
La obsolescencia de estos dispositivos (DCS) aumenta el riesgo de falta de disponibilidad de unidades de generación, principalmente en centrales térmicas, que tienen un alto grado de desgaste mecánico debido a las altas temperaturas y productos químicos utilizados para la producción de energía eléctrica [21].
La gestión en mantenimiento procura reducir costos asociados al mantenimiento, en particular horas/hombre, y costos de reparación. Varias metodologías han sido empleadas para el logro de estos objetivos, tales como TPM (Total Productive Maintenance), RCA (Root Cause Analysis), mantenimiento preventivo, entre otras otros. [22].
El sector eléctrico mundial ha venido afrontando una serie de reformas estructurales muy importantes desde hace más de 20 años. En términos generales, tales reformas tienen como objetivo fundamental el incremento en la eficiencia de la producción de energía aumentando la calidad en el servicio a precios cada vez más competitivos. [23].
Tal renovación / actualización ofrece la posibilidad de utilizar nuevos sistemas DCS basado, principalmente en el libre flujo de datos en tiempo real sin la necesidad de integrar cualquier interface en las arquitecturas de software propietarias como ha sido la práctica hasta ahora [24].
2. Etapas en la realización de la investigación
La investigación se llevó a cabo en cuatro etapas, comenzando con un estudio a fondo de la literatura nacional e internacional sobre el tema objeto de la investigación, para conocer y profundizar en las causas que pueden conducir al fracaso y el tiempo de inactividad inesperado de los equipos, así como sobre los métodos y las técnicas que se pueden aplicar para cumplir con los objetivos propuestos. Un requisito inicial para el desarrollo de estas etapas es la comprensión general del sistema de producción y los datos de consumo de energía y la producción [25].
La segunda fase tuvo lugar la semana siguiente con la entrevista al líder de la actividad de mantenimiento en la empresa, el diagnóstico de dificultades para controlar los fallos del equipo. También se realiza en esta etapa, el estudio documental de las carpetas y las reglas rutinas de mantenimiento, informes de mantenimiento preventivo registro para obtener la base fundamental en la preparación de la lista de verificación (checklist), que se aplicó posteriormente para satisfacer el cumplimiento de las cuestiones expuestas en el ámbito nacional e internacional y detectar las causas de posibles ocurrencias de hechos indeseables.
El tercer paso consistió en la aplicación de la técnica de observación simple directa, realizada durante la tercera semana de investigación de los motores, los equipos auxiliares y generadores, junto con la observación del medio ambiente bajo estudio, que dio cuenta de la realidad expresada en el momento.
En el cuarto paso fueron propuestas las medidas que permitieron el seguimiento de los equipos elegidos para el análisis de vibración, análisis de aceite y la termografía.
• Las aplicaciones se realizaron en cuatro etapas
Etapa 1 - Diagnóstico: Realizado, por el consultor en las áreas de operación donde se implementará el programa, con el objetivo de obtener los datos de operación, entrevistas y análisis de documentos que son la base del Plan Maestro Estratégico de la segunda etapa. Después de realizar los diagnósticos, se presentó a la Directoria y la Administración de la empresa, un informe de los datos recogidos, oportunidades y recomendaciones para el análisis, la discusión y aprobación de las adaptaciones.
Etapa 2 - Plan Maestro Estratégico: El Plan Maestro Estratégico contempla las oportunidades y los objetivos definidos y aprobados en el informe de diagnóstico presentado en la Etapa 1 Preparado por el Consultor, para la presentación, el análisis, la adaptación y la aprobación por los directivos y la Gerencia de la empresa y las personas involucradas en el programa para determinar las necesidades y objetivos específicos de las áreas en las que se ejecutará el programa.
Etapa 3 - Formación: Necesario para nivelar el conocimiento de los participantes, que serán los responsables de la elaboración del programa interno, funciones líderes, coordinadores y miembros del Comité de Dirección.
Etapa 4 -Seguimiento: El programa de seguimiento fue realizado por el consultor de conjunto con el Coordinador General del Programa, incluyendo reuniones con los coordinadores de Pilar, auditorías durante las etapas y orientación de las actividades de aplicación, conceptos, hipótesis y metodología del Plan Maestro Estratégico aprobado. Las actividades previstas y recomendadas para cada pilar se desarrollarán internamente por los Coordinadores y los grupos de trabajo, siendo el consultor el responsabilizado por las auditorias y recomendaciones necesarias durante el período especificado en el contrato.
3. Estudio de caso
El estudio de caso describe los problemas de mantenimiento correctivo que estaban ocurriendo constantemente en equipos de la planta. Por lo tanto, se realizó una investigación con el fin de identificar la causa raíz de paradas de la unidad generadora, siendo necesario obtener alguna información técnica durante el período hasta que se produjo el daño: Análisis de las alarmas y eventos / temperatura del aceite lubricante / Contenido de agua en el aceite lubricante / contenido de metales en el aceite lubricante. A partir de las observaciones derivadas del estudio de caso, que diagnosticó un problema constante en la operación de un motor de Eletrobras Amazonas Energia, la metodología considerada en este trabajo se aplicó en dos etapas, la primera, la implementación de un mantenimiento predictivo y la segunda la aplicación del TPM. Los resultados de la aplicación de la metodología en el estudio de caso se presentan a continuación. La generación es con motores diesel (Wartsila), compuesto por 10 máquinas, que operan a 13,8 kV, teniendo como valores nominales, una potencia aparente de 20.795 MVA.
4. Resultados de la aplicación de GPM
El mantenimiento predictivo y los dispositivos usados en la mayoría de las veces para establecer la necesidad de mantenimiento fue la inspección periódica. Los intervalos de inspección varían en gran medida y también son diferentes para diferentes tareas. Por ejemplo, fueron reportados intervalos que van desde 1 semana a 5 años con entradas más frecuentes de 1 mes. Lo mismo para la parte C. En la parte A, las inspecciones anuales fueron más frecuentes. Otra vía de detección de necesidades de mantenimiento es el monitoreo continuo. Esto fue mencionado con más frecuencia en la parte A (fugas de aceite, la vibración, la temperatura del cojinete) y en menor medida para equipos menos relevantes (condición de conmutación, la corrosión, alta tensión). Se encontró que las herramientas de diagnóstico más eficaces para ser aplicadas en la parte A son el análisis de aceite, pruebas de sobretensión, monitoreo de vibración; en la Parte B, el factor de análisis de imágenes por el poder las pruebas, ensayos térmicos, pruebas dieléctricas; En la Parte C, pruebas de resistencia.
4.1. Análisis de vibraciones
Analizador de vibraciones mod. CMVA60; celerómetro CMSS787A 100 mV / g de la SKF número de serie 13259; Software Prisma 4, versión 1.35, de la SKF.
Esta práctica se aplica periódicamente y se utiliza para evaluar la vibración de motores y equipos dinámicos, siendo capaz de detectar si el equipo necesita alineación, equilibrio o intercambio de cojinete o partes. La clasificación adoptada para la severidad de la vibración es una función de la potencia de accionamiento, la velocidad de rotación de la máquina, así como el nivel crítico para la producción. Cada conjunto se evaluó cuidadosamente para que los niveles de vibración fueran compatibles y registrados con la máxima fidelidad en el Software Prisma 4, con el objetivo de gerenciar y controlar los valores para el análisis de los puntos de acuerdo con la Fig. 1.
De acuerdo a las normas ISO 10816-6 e ISO 8528-9, podemos clasificar los motores y generadores instalados en la planta Mauá, pertenecientes al grupo 3 de la tabla estándar ISO 10816-6. Siguiendo esta tabla, encontramos que los niveles de vibración deben ser inferiores a 18 mm/ s (rms) lo que resulta satisfactorio para el funcionamiento sin restricciones durante largos períodos. En el análisis de los valores de la tabla, se observa que ninguno de los puntos de medición supera el límite de 18 mm/s (rms), por lo que podemos decir que los generadores están en buen estado, siendo clasificados como SATISFACTORIO para el funcionamiento y uso.
4.2. Análisis del contenido de agua en el aceite lubricante
Los resultados de los análisis del contenido de agua (Fig. 2), tomadas periódicamente, como mantenimiento predictivo, muestran niveles normales debido a que valores inferiores a 0,3% son tolerables.
Para este análisis con solo 100 ml de muestra del aceite lubricante del Carter es suficiente, el que se vierte en un frasco de 150 ml. El exceso de lubricante después de la recolección se debe eliminar de inmediato para evitar que las partículas se precipiten. El espacio de 50 ml que representa un 1/3 del mismo se deja vacio lo que permite la posterior agitación de la muestra. La determinación de la presencia de agua en el aceite lubricante puede ser determinada a través de los métodos de control de turbidez en aceites ligeros, crepitación en placa caliente. El método que se utilizó en este estudio es la destilación, que evalúa las características de la volatilidad del aceite de lubricante.
La prueba se hace tomando 100 ml de producto de la muestra que se colocan en un matraz que después se somete a calor para la destilación en condiciones controladas. El calentamiento de los productos provoca la evaporación colectándose el condensado en una probeta de vidrio que se sumerge en un baño de hielo. Después de esta operación las temperaturas registradas son corregidas teniendo en cuenta las pérdidas que se producen en la evaporación de pequeñas partes del producto.
4.3. Análisis de contenido de metal en el aceite lubricante
Los métodos describen el análisis de fluoruro - Metodología de análisis de metales en aceites y grasas para la determinación de metales en el aceite lubricante. Los análisis se realizaron por ferrografía para la lectura directa (hierro y cobre), basado en la extracción de partículas contaminantes magnetizables contenidas en el lubricante, a través de la acción de un campo magnético. El equipo utilizado distribuye las partículas de acuerdo a su tamaño, mientras menor es, menor será la distancia recorrida dentro del campo magnético. Las partículas no magnéticas son "fijas" a una distancia mayor, este patrón se refiere a partículas mayores de 2,5 a 15 micras en un volumen de 100 ml de partículas. El número de partículas mayores a de 2 a 5 micras se utiliza como punto de referencia para las partículas sedimentadas. Las partículas mayores de 15 micras, contribuyen en gran medida a un posible fallo catastrófico de algún componente. Después del análisis, fueron obtenidas las Figs. 3 y 4.
4.4. Termografía
Medición en sistemas eléctricos de baja o alta tensión: las variaciones de temperatura provocadas por el exceso de corriente eléctrica en sistemas de baja tensión pueden ser detectadas por la cámara termográfica. El desequilibrio eléctrico puede ser provocado por diferentes causas: problema de suministro, baja tensión en una fase o falla en la resistencia de aislamiento dentro del bobinado del motor.
Este artículo analiza las causas de sobrecalentamiento en nuestra planta termoeléctrica, así como las pruebas y las herramientas utilizadas con mayor frecuencia para revelar problemas de sobrecalentamiento. Se realizaron pruebas en un sistema eléctrico de baja tensión.
5. Resultados de la ejecución de TPM
El seguimiento de los indicadores se llevó a cabo durante un período de 12 meses, lo que permitió analizar las ventajas de la aplicación de las herramientas del TPM en la empresa. El análisis de los resultados de cada pilar que se describe en la metodología, demostraron los avances significativos logrados con la adopción del TPM, como se describe a continuación.
• Pilar de Educación y Formación
Todos los empleados que participan en el programa se sienten identificados para recibir la Formación Básica en TPM, impartido por los Coordinadores Pilares. Materiales didácticos para la formación básica, aprobados por el comité de la directoria y puestos a disposición de las entidades aseguradoras de los Pilares del TPM. Una planificación más rigurosa de los entrenamientos con el calendario actualizado que se llevó a cabo con los datos relativos a los empleadosa ser entrenados, con fechas definidas e instructores capacitados. Divulgación actualizada constantemente, cantidad de personal y las horas de formación de capacitación realizada. Habilidades de cálculo y clasificación de operadores y equipos de mantenimiento actualizados por el departamento de recursos humanos, indicaciones de la formación básica y específica necesaria para la empresa. La planificación de la capacitación indicada en el párrafo anterior, incluyendo conferencias. Reuniones celebradas sobre TPM dentro de los estándares aprobados, con actas, con el tiempo, temas de la agenda, etc. Tabla de Gestión de TPM aprobado y actualizado, con la información con el personal involucrado incluido en el programa.
• Pilar de mejorías específicas
Grupo de Trabajo formado, Flujo Operacional de una manera clara y didáctica, los equipos, las prioridades y los principales riesgos identificados son conocidos por todos los participantes. Motores, equipos auxiliares y peraciones identificadas por sus capacidades nominales y reales. Criterio para analizar e identificar las principales pérdidas de operación, la estratificación de Pareto (como muestran las Figs. (9, 10, 11 y 12). En espina de pescado (Fig. 5). La metodología a utilizar para investigar y eliminar las pérdidas. Plan de acción (de acuerdo con la Tabla 1 Muestra secuencial del control de etiquetas y Tabla 2. El Plan de acción y control de ejecución de la tarea.), preparado por las acciones del grupo de trabajo, responsables, plazos y avance de las actividades. Poner en marcha el Plan de Acción y comparar los resultados antes y después. Completar el Estándar operacional a ser utilizado por los operadores en cada motor y los equipos auxiliares. Rendimiento de operación /Motor y equipos auxiliares que se evalúa a través de la comparación de los indicadores y los objetivos establecidos para cada motor / Planta. La información sobre los informes de operaciones que se presentan con calidad y supervisados por los Gerentes, Supervisores y Operadores. Los resultados fueron evaluados continuamente por los Gerentes, Supervisores y Operadores. El antes y el después, incluyendo la ganancia de materiales y financiera, etc. Operadores capaces de identificar cualquier distorsión en de los indicadores operacionales. Normas de operación supervisadas por los gerentes, supervisores y operadores.
Operación monitoreada continuamente por los operadores y actuando dentro de las especificaciones de causa y efecto, diagrama de Ishikawa, como se muestra en la Fig. 5, y la Fig. 6 muestra el modelo de etiquetas. Procedimiento adoptado para la colocación del etiquetado, como muestra la Tabla 1 y las acciones y procedimientos a ser adoptados para la retirada del etiquetado como se muestra en la Tabla 2. Es explicado el procedimiento y el control secuencial de etiquetas y el control de la ejecución del Plan de Acción, Figs. 7 y 8.
• Pilar Mantenimiento Autónomo
En la limpieza inicial los operadores deben ser entrenados e involucrados para identificar anomalías en Pilar Mantenimiento Autónomo. En la limpieza inicial los operadores deben ser entrenados e involucrados para identificar anomalías en los motores, equipos auxiliares, las instalaciones y el lugar de trabajo a través de las etiquetas como se muestra en la Fig. 6. áreas, motores, equipos e instalaciones auxiliares deberán estar limpias y mantenerse en estas condiciones, no tolerar ninguna señal de desorganización y falta de higiene. Uso de las 5S. Los sitios que no cumplen con este requisito, al menos, se indicarán con las etiquetas y la reparación futura debe ser incluida en un plan de acción con el tiempo y la responsabilidad como se indica en los cuadros 1 y 2. Después de la colocación de Etiquetas, debe ser creado un controle indicando: El tipo de problema, el número de etiquetas colocadas y removidas y las áreas involucradas en las anomalías, tales como: mantenimiento, operación, seguridad y medio ambiente. Los operadores tienen la obligación de comprobar siempre las condiciones ideales de los motores y equipos auxiliares, el personal siempre debe inspeccionar los locales y zonas de trabajo, siempre se marcan con los colores de la seguridad industrial, placas de identificación, la iluminación y la limpieza. Indicadores de etiquetas actualizados, lo que indica el volumen de etiquetas retirado y colocado en el mes. Todas las actividades antes mencionadas se llevan a cabo con la correcta identificación de zonas de difícil acceso, la eliminación de las fuentes de suciedad y la preparación de los Estándares Provisionales de limpieza, lubricación, inspección, seguridad y medio ambiente.
• Plan Maestro de Mantenimiento Autónomo.
Estructuración del Pilar Mantenimiento Autónomo que aparece en el organigrama de la planta. Determinar cómo identificar anomalías (Identificación por etiquetas). Formación del grupo de trabajo en el procedimiento de etiquetado. Determinar la forma de hacer la limpieza inicial. Establecer la forma de controlar las etiquetas. Iniciar el proceso de etiquetado. INFORME de KPI (número de etiquetas utilizadas). Iniciar proceso de retirada de las etiquetas. Informar a través e KPI el número de etiquetas retiradas. Realizar auditorías internas para asegurar el éxito del programa.
• Pilar de Mantenimiento Programado.
Hoja de Trabajo con las prioridades que contenga las preguntas pertinentes sobre las áreas involucradas con la operación (Operación, Mantenimiento, Ingeniería y Medio Ambiente). Reunión para evaluar y clasificar en A, B y C, todos los motores, equipos e instalaciones auxiliares de la empresa, que se llevan cabo con todas las áreas involucradas. Todos los motores, equipos e instalaciones auxiliares, que se clasifican como A, B y C (Gerenciamiento de Inventario según clasificación), (A) es más importante que no puede faltar en la acción, (B) intermedia, que debe contener al inventario (C) inventario mínimo.El equipo de mantenimiento debe llevar a cabo la inspección de la planificación de la operación en todos los equipos catalogados, el mantenimiento debe realizar una revisión de los motores y el equipamiento de las instalaciones para verificar el cumplimiento con las normas de mantenimiento de acuerdo a como lo define el fabricante para restituirle las condiciones de funcionamiento deseadas. Plan de acción conteniendo lo siguiente: Actividades, materiales, plazos, previstos en cada actividad de reparación y mantenimiento, equipo de mantenimiento en las instalaciones de acuerdo a su clasificación A, B y C y el tipo de mantenimiento recomendado en el plan de mantenimiento. Realizar la planificación y cronograma de las actividades de mantenimiento a realizar para los motores, equipamientos auxiliares y motores. Realizar el informe de las actividades concluidas e iniciadas. Ingeniería debe realizar un análisis crítico de los diagramas de Pareto referido a las fallas como muestran las Figs. 9, 10, 11 y 12 los nuevos informes indicando MTBF y MTTR (de acuerdo con las Tablas 6 y 7 y en la Fig. 12) por motor.
5.1. Análisis de los indicadores
Para facilitar se utilizó el análisis de la evolución de los resultados como las Tablas 3, 4, y 5 (de acuerdo con las Figs. 1a y las Tablas (3, 4, 5, y 8) presentan los valores consolidados de cada uno de los indicadores utilizados, centrándose en los resultados antes y después de la implementación de TPM y la aplicación de MP
Por consiguiente, se ha tratado de demostrar las mejoras obtenidas en el área de mantenimiento de acuerdo a los resultados de MTBF y MTTR.
MTBF es un valor asignado a un dispositivo o aparato para describir su fiabilidad en particular. Este valor asignado indica cuándo se puede producir un fallo en el dispositivo en cuestión. Cuanto mayor sea este indicador, mayor fiabilidad de los equipos y, en consecuencia, el mantenimiento será evaluado en términos de eficiencia.
MTTR es una medida básica del mantenimiento de elementos reparables. Representa el tiempo medio necesario para reparar un componente que ha fallado en las Tablas 6 y 7.
5.2. Formulaciónmatemática
• Cálc. porcentaje de fallas enero de 2013 (Tab.5 y Fig. 10).
• Cálculo del porc.de fallas enero, (Tabla 5 y Fig. 11).
• Cálc.total de ocurr.de fallas ene de 2013 (Tab. 4 y fig. 8).
• Cál.total de ocurr.de fallas ene de 2014(Tab.4 y Fig. 9).
• Cálc.totaltiemp.de parada ene de 2013(Tab. 5 y Fig. 10).
• Cálc. Total tiemp.de parada enero de 2014 (Tab.5 y Fig. 11).
• Cálculo del MTBF 2013 (Cuadro 6)
• Cálculo del MTTR 2013 (Cuadro 6).
• Cálculo del MTBF 2014 (Cuadro 7)
• Cálculo do MTTR 2014 (Cuadro7).
- Cálculo de MTBF ENERO 2013 - 279,06
- Cálculo de MTTR ENERO 2013 - 5,66
- Cálculo de MTBF Enero 2014 - 322,09
- Cálculo de MTTR Enero 2014 - 1,99
Se encontró la ganancia real del MTBF, 322.9 después de la implantación del MP y el TPM como muestran los valores de enero 2014 en comparación con enero de 2013. La Disminución de MTTR, 1,99 después de la aplicación de MP y programa de TPM como se muestra por los valores de enero 2014 en comparación con enero de 2013, Fig. 13.
• Cálculo del porcentaje de fallas, 2013 para la elaboración de (Fig. 17).
Con el análisis de los resultados y discusión de los hechos fue verificado que La implantación del TPM y MP
es viable económicamente como muestra el aumento del MTBF y la disminución del MTTR. Además fue verificado un aumento del mantenimiento autónomo realizado por los operadores, un aumento de las actividades predictivas y disminución del mantenimiento correctivo, las Figs. 17 y 18.
6. Costos ligados a los mantenimientos en la planta termoeléctrica de MauáManaus-Amazonas-Brasil.
Tablas 9, 10 y 11 presentan un estudio de los costes directos de mantenimiento correctivo de los diez motores y generadores de la central eléctrica de Mauá, incluidos los costos de sustituir la energía generada por las centrales termoeléctricas en Manaus - AM.
7. Conclusiones
Con base en la información del estudio de caso de Eletrobras Amazonas Energía, fue posible identificar las posibles causas de parada de los equipos. Se dio solución a un problema real de la empresa, lo que reporto ganancias. Una vez detectado los problemas el área de mantenimiento de la empresa propuso la aplicación, primero, de un programa de mantenimiento predictivo; y en una segunda etapa, la aplicación de un programa de mantenimiento productivo total. Después de las implementaciones de los programas, se ha demostrado, a través de la mejora de los indicadores de mantenimiento, la solución de un problema en una situación real con la continua disminución de mantenimiento correctivo en un año en la empresa Eletrobras Amazonas Energía.
Con poca inversión, podemos resolver el problema del mantenimiento correctivo en nuestra planta sin afectar la producción de energía eléctrica de la planta de forma segura y eficaz, sin causar más daños al medio ambiente, manteniendo al mismo tiempo la fiabilidad del sistema eléctrico de Manaus, sin comprometer la seguridad de las instalaciones, a un costo menor de U$ 7,854.095,91 gastados anualmente.
Agradecimientos
ITEGAM, FAPEAM y ELETROBRAS
Referencias
[1] Barlow, R.E. and Proschan, F., Statistical Theory of reliability and life testing. New York: Holt, Rinehart and Winston, Inc., 1975.
[2] Anders, G.J., Probability concepts in electric power systems. New York: J. Wiley & Sons, 1990.
[3] Zheng, X. and Fard, N., A maintenance policy for repairable systems based on opportunistic failure-rate tolerance, IEEE Trans. Reliability, 40(2), pp. 237-244, 1991. DOI: 10.1109/24.87134..
[4] Ebrahimi, N., Two new replacement policies, IEEE Trans. Reliability, 42(1), pp. 141-147, 1993.
[5] Arango-Serna, M.D., Enterprise arquitecture as tool for managing operational complexidy in organizations. DYNA, 81(185), pp. 219-226, 2014. DOI: 10.15446/dyna.v81n185.41928
[6] Canfield, R.V., Cost optimization of periodic preventive maintenance, IEEE Trans. Reliability, 35(1), pp. 78-81, 1986. DOI: 10.1009/TR1986.4335355
[7] Endrenyi, J. and Sim, S.H., Availability optimization for continuously operating equipment with maintenance and repair, in Proceedings of the Second PMAPS Symposium, Sept. 1988, Nov. 1989, EPRI Publication EL-6555.
[8] Anders, G.J. et al., Maintenance planning based on probabilistic modeling of aging in rotating machines, in CIGRE Conference, Paris, 1992, Paper No. 11-309.
[9] Reichman, B. et al., Application of a maintenance planning model for rotating machines, in CIGRE Conference, Paris, 1994, Paper No. 11-204.
[10] Jardine, A.K.S., Maintenance, replacement and reliability. London: Pitman Publishing, 1973.
[11] Reliability Centered Maintenance Seminar. New York: A publication of the Consolidated Edison Company, 1988.
[12] Smith, A.M., Reliability-centered maintenance. New York: McGraw-Hill, Inc., 1993.
[13] Moubray, J., Reliability-centered maintenance. New York: Industrial Press Inc., 1992.
[14] Wisconsin Public Service Corp., PM optimization boosts reliability at small cost, Utility Best Practices, 157 P., 1995.
[15] Ascher, H. and Feingold, H., Repairable systems reliability. NewYork: Marcel Dekker, Inc., 1984.
[16] Valdez-Flores, C. and Feldman, R.M., A survey of preventive maintenance models for stochastically deteriorating single-unit systems, Naval Research Logistics Quarterly, 36, pp. 419-446, 1989.
[17] EPRI, Probabilistic model to estimate the remaining life of generator station components, Report RP-2577-1, 1993.
[18] Endrenyi, J., Anders, G.J. and Leite da Silva, A.M., Probabilistic evaluation of the effect of maintenance on reliability-An application, IEEE Trans. Power Systems, 13(2), pp. 576-583, 1998. DOI: 10.1109/59.667385.
[19] Billinton, R. and Pan, J., Optimal maintenance scheduling in a parallel redundant system of series components in each branch, IEEE Trans. Power Systems, to be published, 1999. DOI: 10.1109/61.772336.
[20] Dialynas, E.N. and Michos, D.G., Time-dependent unavailability analysis of standby components incorporating arbitrary failure distributions and three inspection/maintenance policies, Reliability Engineering and System Safety, 39, pp. 35-54, 1993. DOI: 10.1016/0951-8320(93)90146-P
[21] Decker, D.L., What is in store for DCS systems? Where are they headed? Pulp and Paper Industry Technical Conference, 2001 Conference Record of. pp.17-20, 2001.
[22] Quiroga-Méndez, J. and Oviedo-Castillo, S. Implementing condition- Implementing condition-based maintenance using modeling and simulation: A case study of a permanent magnet synchronous motor. Ingeniería e Investigación. 31(2), pp. 18-28, 2011.
[23] Gallego-Vega L.E. and Duarte-Velasco, O.G., The effect of electric transmission constraints on how power generation companies bid in the Colombian electrical power market. Ingeniería e Investigación, 30(2), pp. 62-77, 2010.
[24] Chen, L., A framework of a web-based distributed control system. Master of Science Thesis, Department of Electrical and Computer Engineering, University of Calgary, Calgary, Canada, 2003, 113 P. DOI: 10.1109/CCECE.2003.1226150
[25] Castrillón, R,P., González, A.J. y Quispe, E.C., Mejoramiento de la eficiencia energética en la industria del cemento por proceso húmedo a través de la implementación del sistema de gestión integral de la energia, DYNA, 80(177), pp. 115-123, 2013.
M. Fonseca-Junior, es MSc. en Ingeniería Eléctrica en 2012, de la Universidad Federal de Pará (UFPA), Brasil. Eng. de la empresa de Ingeniería Eléctrica Eletrobras. Cursa el Doctorado en Ingeniería Eléctrica (UFPA). ORCID: 0000/0001/6001/3098
U. Holanda-Berzerra, es Dr. en Ingeniería Eléctrica en 1988, de la Universidad Federal de Rio de Janeiro (COPPE / UFRJ), Brasil. Es profesor en el Departamento de Ingeniería Eléctrica e Informática UFPA desde 1977. ORCID: 0000/0002/2853/8676.
J. Cabral-Leite, es Dr. en Ingeniería Eléctrica en 2013 de la Universidad Federal de Pará (UFPA), Brasil.Profesor e Investigador de ITEGAM. Manaus. Amazonas. Brasil. ORCID: 0000/0002/1337/3549.
T.L. Reyes-Carvajal, es Dr. en Ingeniería Mecánica en 1997 de la Universidad Central de las Villas, Cuba. Profesor e Investigador de ITEGAM. ORCID: 0000/0003/4699/0719
Cómo citar
IEEE
ACM
ACS
APA
ABNT
Chicago
Harvard
MLA
Turabian
Vancouver
Descargar cita
CrossRef Cited-by
1. Jonathan David Morales Méndez, Ramon Silva Rodriguez. (2017). Total productive maintenance (TPM) as a tool for improving productivity: a case study of application in the bottleneck of an auto-parts machining line. The International Journal of Advanced Manufacturing Technology, 92(1-4), p.1013. https://doi.org/10.1007/s00170-017-0052-4.
2. Orlando Duran, Andrea Capaldo, Paulo Duran Acevedo. (2017). Lean Maintenance Applied to Improve Maintenance Efficiency in Thermoelectric Power Plants. Energies, 10(10), p.1653. https://doi.org/10.3390/en10101653.
3. Edwin Edgardo Espinel-Blanco, Juan Carlos Hernandez-Criado, Torcoroma Velásquez- Pérez. (2016). Programa de gestión de mantenimiento para una flota de vehículos de transporte de productos avícolas. Revista Ingenio, 11(1), p.9. https://doi.org/10.22463/2011642X.2089.
4. Jānis Krūmiņš, Māris Kļaviņš. (2023). Investigating the Potential of Nuclear Energy in Achieving a Carbon-Free Energy Future. Energies, 16(9), p.3612. https://doi.org/10.3390/en16093612.
Dimensions
PlumX
Visitas a la página del resumen del artículo
Descargas
Licencia
Derechos de autor 2015 DYNA

Esta obra está bajo una licencia internacional Creative Commons Atribución-NoComercial-SinDerivadas 4.0.
El autor o autores de un artículo aceptado para publicación en cualquiera de las revistas editadas por la facultad de Minas cederán la totalidad de los derechos patrimoniales a la Universidad Nacional de Colombia de manera gratuita, dentro de los cuáles se incluyen: el derecho a editar, publicar, reproducir y distribuir tanto en medios impresos como digitales, además de incluir en artículo en índices internacionales y/o bases de datos, de igual manera, se faculta a la editorial para utilizar las imágenes, tablas y/o cualquier material gráfico presentado en el artículo para el diseño de carátulas o posters de la misma revista.