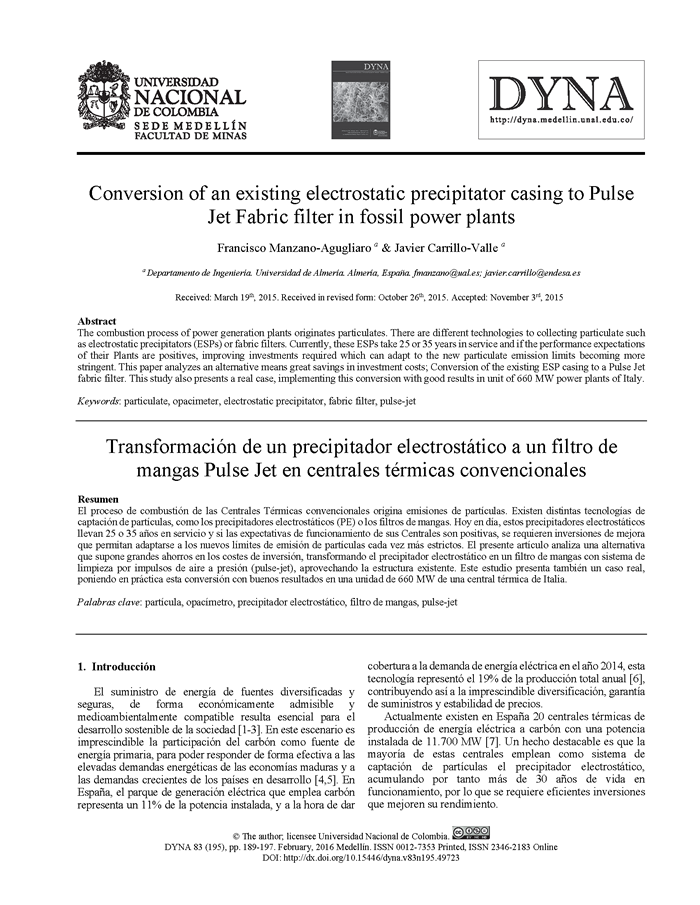
Publicado
Conversion of an existing electrostatic precipitator casing to Pulse Jet Fabric filter in fossil power plants
DOI:
https://doi.org/10.15446/dyna.v83n195.49723Palabras clave:
particulate, opacimeter, electrostatic precipitator, fabric filter, pulse-jet (es)DOI: https://doi.org/10.15446/dyna.v83n195.49723
Conversion of an existing electrostatic precipitator casing to Pulse Jet Fabric filter in fossil power plants
Transformación de un precipitador electrostático a un filtro de mangas Pulse Jet en centrales térmicas convencionales
Francisco Manzano-Agugliaro a & Javier Carrillo-Valle a
a Departamento de Ingeniería. Universidad de Almería. Almería, España. fmanzano@ual.es; javier.carrillo@endesa.es
Received: March 19th, 2015. Received in revised form: October 26th, 2015. Accepted: November 3rd, 2015
This work is licensed under a Creative Commons Attribution-NonCommercial-NoDerivatives 4.0 International License.
Abstract
The
combustion process of power generation plants originates particulates. There
are different technologies to collecting particulate such as electrostatic
precipitators (ESPs) or fabric filters. Currently, these ESPs take 25 or 35
years in service and if the performance expectations of their Plants are
positives, improving investments required which can adapt to the new
particulate emission limits becoming more stringent. This paper analyzes an
alternative means great savings in investment costs; Conversion of the existing
ESP casing to a Pulse Jet fabric filter. This study also presents a real case,
implementing this conversion with good results in unit of 660 MW power plants
of
Italy .
Keywords: particulate, opacimeter, electrostatic precipitator, fabric filter, pulse-jet
Resumen
El proceso de combustión de las Centrales Térmicas
convencionales origina emisiones de partículas. Existen distintas tecnologías
de captación de partículas, como los precipitadores electrostáticos (PE) o los
filtros de mangas. Hoy en día, estos precipitadores electrostáticos llevan 25 o
35 años en servicio y si las expectativas de funcionamiento de sus Centrales
son positivas, se requieren inversiones de mejora que permitan adaptarse a los
nuevos límites de emisión de partículas cada vez más estrictos. El presente
artículo analiza una alternativa que supone grandes ahorros en los costes de
inversión, transformando el precipitador electrostático en un filtro de mangas
con sistema de limpieza por impulsos de aire a presión (pulse-jet),
aprovechando la estructura existente. Este estudio presenta también un caso
real, poniendo en práctica esta conversión con buenos resultados en una unidad
de 660 MW de una central térmica de Italia.
Palabras clave: partícula, opacímetro, precipitador electrostático, filtro de mangas, pulse-jet
1. Introducción
El suministro de energía de fuentes diversificadas y seguras, de forma económicamente admisible y medioambientalmente compatible resulta esencial para el desarrollo sostenible de la sociedad [1-3]. En este escenario es imprescindible la participación del carbón como fuente de energía primaria, para poder responder de forma efectiva a las elevadas demandas energéticas de las economías maduras y a las demandas crecientes de los países en desarrollo [4,5]. En España, el parque de generación eléctrica que emplea carbón representa un 11% de la potencia instalada, y a la hora de dar cobertura a la demanda de energía eléctrica en el año 2014, esta tecnología representó el 19% de la producción total anual [6], contribuyendo así a la imprescindible diversificación, garantía de suministros y estabilidad de precios.
Actualmente existen en España 20 centrales térmicas de producción de energía eléctrica a carbón con una potencia instalada de 11.700 MW [7]. Un hecho destacable es que la mayoría de estas centrales emplean como sistema de captación de partículas el precipitador electrostático, acumulando por tanto más de 30 años de vida en funcionamiento, por lo que se requiere eficientes inversiones que mejoren su rendimiento.
El precipitador electrostático está formado por una estructura soporte externa dividida en una serie de campos o secciones que recibe los gases de combustión a un temperatura de 100°- 220°C y utiliza la fuerza electrostática para separar las partículas de los gases de combustión que las arrastran [8]. Los gases de combustión se hacen pasar por una cámara que contiene placas de acero (electrodos colectores) colocadas verticalmente, en la dirección paralela al flujo de los gases, formando entre ellas una serie de pasillos. En cada pasillo existen un conjunto de alambres verticales (electrodos de descarga\emisores) situados en un plano paralelo y equidistantes de las placas que están soportados por una estructura única [9].
Esta estructura se apoya en aisladores para que quede aislada eléctricamente del resto de los componentes, los cuales están conectados a tierra. La estructura aislada que soporta todos los electrodos de descarga está alimentada con una tensión continua negativa, que puede alcanzar valores de 45/70kV, desde un conjunto transformador-rectificador [10]. Como los electrodos colectores o placas están conectadas a tierra, se crea un campo eléctrico intenso entre los electrodos de descarga y las placas.
El gas está formado normalmente por moléculas neutras y su movimiento no se ve afectado por el campo eléctrico, sin embargo, siempre existe alguna molécula ionizada, ya sea por radiación electromagnética o como consecuencia de elevadas temperaturas [9]. Estas moléculas ionizadas (iones gaseosos) y los electrones separados de ellas se mueven hacia los electrodos de polaridad opuesta, donde se descargan. Es decir, se crea una corriente eléctrica, pero ésta es tan débil que casi no puede ser detectada por los aparatos de medida. Si se aumenta el voltaje aplicado a los electrodos, la intensidad del campo en las proximidades del emisor aumenta hasta el punto que los iones y electrones son acelerados pudiendo provocar la ionización de otras partículas neutras por impactos con ellas, y si se repite con una determinada frecuencia de forma que se generen una gran cantidad de iones y electrones libres en la zona próxima al electrodo emisor, se produce una descarga eléctrica, denominada efecto corona [11]. El gas se ioniza en esta zona y se forma una gran cantidad de iones positivos y negativos. Los iones positivos son atraídos y atrapados inmediatamente por los electrodos de descarga, cargados negativamente. Los iones negativos, sin embargo, tienen que atravesar todo el espacio que hay entre los electrodos de descarga y las placas (electrodos colectores, polo positivo). Por lo tanto hay un flujo de iones negativos desde los electrodos de descarga. En el camino hacia las placas, los iones negativos chocan con las partículas de polvo y se adhieren a ellas [12]. Estas partículas, por tanto, quedan cargadas eléctricamente y comienzan a moverse hacia las placas en la misma dirección que los iones negativos. La fuerza eléctrica que actúa sobre cada partícula es mucho mayor que la fuerza gravitatoria y por tanto su "velocidad de migración" hacia las placa es mucho mayor que la "velocidad de sedimentación" y, si se diseña adecuadamente el precipitador, también será adecuada para competir con la velocidad de arrastre de los gases. El polvo se adhiere a las placas colectoras y mediante golpeo periódico, se hace que la capa de polvo depositada sobre ellas, se desprenda y se deslice hacia una tolva situada en la parte inferior [13].
2. Motivos para de reemplazar o convertir el PE existente en un Filtro de Mangas
Existen varios factores que inciden de manera significativa sobre el rendimiento de los PE, y que justifican la opción de reemplazarlos o convertirlos en un Filtro de Mangas, y que se detallan a continuación.
2.1. Envejecimiento del equipo
EL PE instalado en una central térmica típica de carbón se espera que permanezca en funcionamiento durante varias décadas, sobre todo teniendo en cuenta que la vida útil media de una central son 30 años [13]. A lo largo de los años, es normal realizar intervenciones de mantenimiento programado para remplazar componentes internos, tales como martillos del sistema de golpeo, electrodos de descarga, etc. Sin embargo, llega un momento en el que la mayoría de las placas colectoras necesitan ser sustituidas e incluso los transformadores y/o el sistema de control, con lo que la inversión se hace tan elevada que llegamos al punto en el que la conversión a otra alternativa es viable [14].
2.2. Límites de emisión más restrictivos
El consumo de combustibles fósiles se traduce en un aumento de la contaminación ambiental debido a la emisión de CO2 y otros gases que causan el calentamiento global a través de lo que se conoce como el efecto invernadero [15,16]. En relación a los limites de emisión de partículas, hasta el pasado día 6/01/2011 ha estado en vigor la Directiva Europea 2001/80/CE de Grandes Instalaciones de Combustión (GIC's) de fecha 23/10/2001, la cual fijaba el límite en 50 mg/Nm3, a las instalaciones con una potencia superior a 50 MW térmicos [17]. Con fecha 17/12/2010 se publicó la nueva Directiva 2010/75/UE de Emisiones Industriales (IED, en inglés), la cual entró en vigor el día 6/01/2011. Esta nueva directiva modificará los términos de emisiones permitidos por la Directiva 2001/80/CE a partir del 01/01/2016. Esta normativa, impone unos valores diferentes en función de la fecha de concesión de permiso y potencia térmica nominal total. Para las instalaciones de combustión a las que se haya concedido permiso antes del 7 de enero de 2013, o para las que sus titulares hayan presentado una solicitud de permiso completa antes de dicha fecha, a condición de que dichas instalaciones hayan entrado en funcionamiento a más tardar el 7 de enero de 2014, los valores límites de emisión de partículas, para una potencia térmica nominal superior a 300 MW serán 20 mg/Nm3. Para las instalaciones no incluidas en las indicadas anteriormente, los valores límites de emisión, con carácter general, para una potencia térmica nominal superior a 300 MW serán 10 mg/Nm3 [18].
2.3. Cambio del tipo de carbón utilizado
Las Centrales térmicas en muchas ocasiones se ven obligadas a cambiar el tipo de carbón que están quemando, por diversos motivos:
- Deterioro de los parámetros de calidad del carbón suministrado por razones geológicas, o simplemente por el cierre de las minas de origen.
- Por estrategias de mercado, de forma que les permitan disminuir los costes de producción [19].
- El fuerte crecimiento de China e India en el mercado del carbón [20].
Estos nuevos carbones pueden penalizar el rendimiento del PE. Normalmente esto ocurre debido a un aumento del porcentaje de cenizas, a un aumento de la resistividad de las cenizas o un aumento de la fineza de las partículas, las cuáles son más difíciles de captar.
2.4. Instalación de Desulfuraciones de los Gases de Combustión (DGCs)
Para el control de las emisiones de los SOx, las grandes instalaciones cuentan con desulfuradoras de los gases de combustión (DGCs), y en la mayoría de los casos son húmedas [21]. Estas desulfuraciones húmedas están normalmente ubicadas aguas a bajo de los PE, y por consiguiente se ven afectadas por la eficacia de éste. Las reacciones químicas que se crean en un sistema DGC con caliza húmeda están caracterizadas por una serie de fases, aunque dichas fases se pueden simplificar con la siguiente reacción global [22], (eq. 1):
El objetivo de las plantas es crear yeso de carácter comercial, cumpliendo con los criterios de calidad de la industria del cemento, para poder venderlo [23]. Si el rendimiento de captación del PE no es adecuado, existirá una gran cantidad de cenizas en el tanque de reacción del absorbedor de la DGC, donde se mezclan con la lechada de caliza existente, por lo que afectan a los parámetros de calidad del yeso (blancura, pureza>80%, humedad libre<10%) [22] que pueden impedir su venta como subproducto, generando problemas de almacenamiento y/o costes de esmaltimento a las centrales.
2.5. Emisiones de metales pesados: Mercurio
Durante la combustión, los metales pesados que contienen la mayoría de los combustibles sólidos son liberados y algunos de ellos pueden llegar a la atmósfera integrados en partículas o en forma de vapor, particularmente el mercurio (Hg) por su elevada volatilidad [19,25].
En relación con el mercurio u otros metales condensables, existe una preocupación creciente, principalmente en Estados Unidos [26], sobre sus potenciales efectos adversos sobre la salud [27], por lo que la Administración norteamericana ha comenzado a legislar para restringir el uso del mercurio en los procesos industriales y reducir los niveles de concentración emitidos a la atmósfera. En Europa se ha comenzado a tomar conciencia de la problemática [28], y también es presumible la aparición de limitaciones en las emisiones de mercurio, sin embargo los PE muestran una caída importante de rendimiento en el entorno de la fracción de partículas de 1 mm, como en el caso de partículas enriquecidas con metales pesados. Para muchas centrales de carbón, la mejor opción actualmente es instalar filtros de mangas con los que se puede conseguir una eficiencia media aproximada de eliminación del Hg del 40% [29]. Esta eficiencia de captura se puede aumentar acondicionando el gas de combustión con pequeñas cantidades de aditivos que se añade al flujo de gas antes de que atraviese el filtro de mangas, alcanzando así valores de eliminación del Hg > 90% [30].
2.6. Control de PM2,5
Las previsiones para un futuro no muy lejano pasan por la introducción de limitaciones no sólo en partículas totales PM10 como actualmente, sino en las fracciones más finas. Las partículas más pequeñas de 2,5 micras PM2,5, presentan un mayor riesgo para la salud [31], además de permanecer mayor tiempo suspendidas en el aire y transportadas a largas distancias [32,33]. A parte de esto, es sobre la superficie de las partículas más finas donde suelen depositarse algunos compuestos condensables como los gases ácidos y los metales, lo que incrementa su riesgo potencial [34].
Las mejoras de rendimiento necesarias en los internos de los PE existentes, para alcanzar los límites de emisión PM2,5 podrían ser tan importantes que la conversión a filtro de mangas seria una opción viable. Debido a las consideraciones actuales y futuras expuestas anteriormente, la transformación de un precipitador electrostático en un filtro de mangas, es un proyecto que ofrece atractivas ventajas y se adapta a las exigencias medioambientales cada vez más estrictas.
Bajo este contexto se ha elaborado el presente artículo, que tiene como objetivo establecer los aspectos fundamentales de diseño e instalación a tener en cuenta a la hora de realizar una completa especificación para transformar un precipitador electrostático en un filtro de mangas, reutilizando la estructura existente y aplicando un sistema de limpieza por impulsos de aire a presión (pulse-jet). Finalmente se ilustra su aplicación, analizando un caso real en una unidad de 660 MW de una Central Térmica de Italia.
3. Propuesta tecnológica
Los filtros de mangas consisten en estructuras metálicas cerradas en cuyo interior se disponen elementos filtrantes textiles en posición vertical. Según el diseño pueden adoptar formas tubulares, y se denominan mangas, o formas rectangulares, y se denominan bolsas. Se montan sobre una cámara o compartimento que acaba en su parte inferior en una tolva de recogida de partículas. Los gases cargados de partículas entran en cada compartimento a través de un difusor, donde pierde velocidad y turbulencia, para distribuirse en toda la longitud del mismo, dejando las partículas más pesadas que se desprenden por gravedad en las tolvas. A continuación, el gas asciende y es forzado a pasar a través de las filas de mangas, atravesándolas del exterior hacia el interior, depositando las partículas sobre la superficie de las mismas. La filtración se produce como resultado de la formación de una capa de polvo primaria en la superficie de las mangas (llamada torta) y de una acumulación de partículas de polvo en el interior del material filtrante, que dependen de la concentración de cenizas en los gases, del estado de las mangas y del caudal de gases. Una vez formada la capa primaria, la penetración se hace muy baja y la filtración se produce por tamizado (filtración superficial). El proceso de filtración continúa hasta que la caída de presión se hace tan importante que requiere la limpieza del sistema [35].
Cada manga es instalada en una estructura (jaula portamangas) para que éstas no colapsen por depresión y permanezcan abiertas durante el proceso de filtrado. Finalmente, todas las jaulas portamangas con sus respectivas mangas, son soportadas verticalmente desde su parte superior en la placa portamangas. Esta placa es el límite de separación entre el gas sucio y el gas limpio, por lo que el único camino del gas para pasar a la zona de gas limpio (walk in plenum), es a través de las mangas. Por tanto, cuando se trata de placa portamangas instalada en un filtro de mangas con reutilizo de la estructura existente del PE es necesario una especial consideración ya que se pueden presentar dilataciones térmicas diferenciales entre los compartimentos y la placa, si son de grandes dimensiones o son de diferentes materiales. Para impedir cualquier fuga de gas sucio a través de la placa y las mangas, los fabricantes de las mismas proporcionan datos para un buen "sellado", aplicando el sistema "snap-band" (pellizco o pliego normal), y su diseño permite la fácil sustitución de las mangas [36]. La selección de las características del tejido filtrante de las mangas es el parámetro más importante a considerar desde el punto de vista de diseño, ya que la operación del filtro está limitada a la temperatura de los gases que resista el material filtrante (actualmente se puede trabajar hasta temperaturas del orden de 250°C); al grado de humedad que puede generar costras sobre las mangas; y al posible ataque químico por sustancias ácidas o alcalinas presentes en los gases. Todo ello disminuye la vida útil de las mangas, aumentando los costes de O&M, con la necesidad de recambio de las mismas. Principalmente existen dos tipos de configuración de los medios filtrantes:
- Tejido hilado (TH): se trata de fibras que son extruidas en diferentes tamaños de hilo y se disponen en una saca tejida. Aquí la captación de partículas es superficial de dentro a fuera; están construidas de fibra de vidrio y/o poliéster, el método de limpieza es aire inverso/vibración y la velocidad de filtrado es baja.
- Fieltro (F): se trata de fibras de ryton, acrilicos, y poliamidas entrelazadas mecánicamente; para mejorar su estabilidad, la mayoría de los fieltros cosidos tienen un elemento soporte en su centro. La captación de partículas es superficial de fuera a dentro; el método de limpieza es Pulse Jet y la velocidad de filtrado es alta.
En EE.UU, el tejido más comúnmente adoptado en centrales térmicas es la fibra de vidrio hilada, aunque con tendencia a la implantación de fieltros cosidos o membranas de politetrafluoroetileno (PTFE), tales como Gore-Tex sobre el vidrio hilado. En Canadá, Australia y Europa, las experiencias principales son con tejidos de fieltro (acrílicos como Dralon T, PPS o Ryton, Nomex, Huyglas, poliamida P84 y teflón). Estos materiales son aplicables para los filtros con método de limpieza por impulsos de aire a presión (Pulse Jet), y se han considerado más adecuados por su coste y fiabilidad [37].
Existen tres tipos de filtros de mangas atendiendo al método de limpieza utilizado:
- Filtro de mangas con limpieza por vibración
- Filtro de mangas con limpieza por aire a contracorriente
- Filtro de mangas con limpieza por impulsos de aire a presión (Pulse Jet).
Sin embargo, la opción más viable a la hora de transformar un precipitador electrostático en un filtro de mangas, reutilizando la estructura existente, es el sistema de limpieza "Pulse Jet", porque ocupan menor área en planta que los sistemas convencionales, adecuando la superficie requerida por las mangas de filtrado en el espacio disponible del precipitador electrostático.
Este sistema durante el ciclo de limpieza, el polvo se desaloja utilizando un impulso de aire comprimido que se inyecta en la parte superior de las mangas filtrantes. Este impulso a alta presión interrumpe el flujo normal del gas a través del filtro y crea una onda que al desplazarse a lo largo de la manga hace que esta se flexione, rompiendo la capa de polvo que cae hacia la tolva. La parte inferior de las mangas está cerrada y el impulso es lo suficiente grande para que pueda desplazarse a lo largo de la manga y regresar a la parte superior.
El impulso de aire de limpieza puede ser suministrado por un compresor o bien por un soplador retráctil, y típicamente el soplado se hace a una fila completa de mangas, a través de una lanza o tubería de soplado que contiene pequeños orificios "boquillas o venturis" para inyectar el aire a alta velocidad en la parte superior de las mangas [37]. Cada lanza está conectada a un tanque de aire a través de una válvula de diafragma. El tanque se mantiene normalmente 2 puntos por encima del valor nominal de la presión de trabajo, y a través de la lógica del ciclo de limpieza, que puede ser por un tiempo preestablecido o por una medida de DP; se energiza la válvula solenoide y se libera el paso a través de la válvula de diafragma, permitiendo el paso de aire a la lanza de soplado. A su vez, el sistema Pulse Jet, se subdivide en 3 tipos de lógica de funcionamiento, que se caracterizan por la presión y el volumen del aire utilizado para la limpieza:
- Alta Presión/Bajo Volumen (HP/LV)
- Media Presión/Medio Volumen (IP/IV)
- Baja Presión/Alto Volumen (LP/HV)
El método Pulse Jet de alta presión y bajo caudal de aire (HP/LV) es mucho más energético, lo que permite relaciones de caudal de gases /superficie de tejido, A/T (m3min-1/m2) o velocidad de filtrado (m/min), mucho mayores que en los sistemas convencionales. Este es el parámetro principal a la hora de dimensionar el filtro, ya que influye sobre el límite de las emisiones, la pérdida de carga del sistema, la frecuencia de los ciclos de limpieza (y por tanto, en la vida útil de las mangas) y en el tamaño necesario del filtro.
Teniendo en cuenta que se pretende reutilizar la estructura existente del precipitador electrostático, un valor elevado de A/T es fundamental, ya que conlleva ocupar menos área de filtrado, asegurando que el espacio disponible es suficiente para albergar las mangas y con ello minimizando las posibles modificaciones de la estructura que impactarían de modo sustancial sobre el coste inicial de la inversión.
4. Aplicación Práctica
Se ilustra la tecnología propuesta, aplicándola al caso real de un precipitador electrostático en la Unidad 4 (660MW) de una Central Térmica de Italia, de modo que nos familiaricemos con el tipo de información requerida y las áreas claves normalmente incluidas en una especificación de este tipo. La conversión fue completada en 12 semanas, en junio del año 2012, aprovechando una Revisión General de Turbina (RGT) de la Unidad.
4.1. Antecedentes
El precipitador electrostático de la unidad 4, es fabricado en el año 1990, y en el año 2002 se realiza una importante intervención de mantenimiento, principalmente en la parte mecánica. Después de una mejora en la eficiencia de captación, ha sufrido un degrado de las prestaciones que no garantizaban la funcionalidad de la unidad en general.
- El Precipitador electrostático existente está formado por dos cuerpos en paralelo separados físicamente; cada cuerpo está compuesto de 14 campos eléctricos. Cada cuerpo está dotado de cámara superior al interno de la cual están ubicados los alimentadores de alta tensión (transformadores-convertidores). En la Tabla 1 se muestran las principales características técnicas del mismo.
- Los Ventiladores de tiro inducido (VTI) tienen: Potencia (7.000 kW), Tensión (6.000 V), N° de polos (8), Intensidad (804,1 A) y Factor de Potencia (0,86).
4.2. Descripción funcional de la transformación a PJFF
El objetivo principal de esta transformación es la de llegar a adecuar la estructura mecánica y la envolvente externa del actual precipitador electrostático, con el fin de reconvertir este sistema de captación de partículas en un filtro de mangas con sistema de limpieza pulse-jet (HP/LV). Los sistemas eléctricos auxiliares serán ubicados en la sala eléctrica del PE, previo desmontaje de los equipos no utilizables. Por otro lado, para poder compensar la mayor pérdida de carga introducida por el filtro, se sustituye el ventilador de tiro inducido (VTI) para aumentar la aspiración. El filtro es proyectado para una vida útil de 25 años, con 8.000 horas de funcionamiento y 50 arranques/paradas al año. El combustible de diseño es 100% carbón, cuya composición puede variar fuertemente en función del origen del suministro en el mercado spot, pero como referencia será carbón sudafricano. El uso de fuel será permitido solo durante el proceso de arranque de la unidad (calentamiento caldera).
4.2.1. Descripción funcional de la transformación a PJFF
La estructura externa de los 2 cuerpos de PE es reutilizada, para ello es inicialmente previsto un lavado interno con agua, para a continuación proceder con las actividades de desmontaje de los siguientes elementos:
- Cámara Superior: sistema de calefacción con vapor, alimentadores de alta tensión (T/R) con toda la conexión eléctrica a los electrodos de descarga, aisladores soporte, techo "caliente" y "frío".
- Internos: electrodos de captación (placas completas), electrodos de descarga con la estructura soporte y el sistema de golpeo (martillos, yunques, motoreductores, etc). En la Fig. 1 muestra un detalle del desmontaje.
La siguiente fase es la construcción de los compartimentos internos a través de la instalación de paredes de separación (con los respectivos refuerzos), que dividen longitudinalmente cada cuerpo/semisección en 2 compartimentos (4 en total). El filtro podrá funcionar también con un compartimento excluso por anomalía o mantenimiento. La interceptación del compartimento se obtiene con la instalación de compuertas de accionamiento neumático al ingreso y a la salida. También, cada compartimento es dotado de un sistema de by-pass realizado a través de un conducto interno, gobernado con una compuerta neumática que mete en conexión el conducto de ingreso de gases con el de salida de los mismos, ver Fig. 2.
Externamente son reutilizados los conductos existentes al ingreso, ver Fig. 3, provenientes de los precalentadores de aire hasta las 4 bocas de entrada, para instalar a continuación:
- Un conducto de transición con rectificadores de flujo, para adquirir la mejor uniformidad del gas al ingreso
- Dos conductos de equilibrio, uno al ingreso y otro a la salida, para meter en comunicación a través de 2 compuertas de regulación neumáticas (posicionables manualmente), los compartimentos centrales B-C que pertenecen respectivamente al cuerpo 2 y 1 del filtro.
4.2.2. Elementos filtrantes: limpieza y producción de aire comprimido
El material base, constituyente de las mangas filtrantes empleadas es fieltro P84/PPS con armadura en PPS y tratamiento superficial PTFE. Este material consiente de operar a una temperatura nominal de 180°C con puntas de corta duración de 200°C, y posee una excelente resistencia a la abrasión, a los ácidos y alcalinos. En la Fig. 4, se muestran las mangas ya instaladas.
La limpieza de las mangas es de tipo pulse-jet, a alta presión y bajo volumen (HP/LV) basado en un sistema de producción y secado de aire comprimido, constituido de 4 compresores y 4 torres de secado (3 en servicio y uno en reserva).
El sistema cíclico de limpieza de las mangas debe ser en servicio cuando la unidad térmica es en funcionamiento, con la sola excepción de la fase de arranque, en la cual viene utilizado gasóleo o fuel y por tanto conviene mantener las mangas revestidas de calcio y/o cenizas para evitar fenómenos de ataque químicos en las mismas. La secuencia de limpieza prevé la posibilidad de utilizar dos velocidades:
- Con baja frecuencia, en la cual el tiempo de pausa entre dos impulsos sucesivos de limpieza (es decir, el tiempo que transcurre entre la limpieza de dos filas de mangas sucesivas) es alto, 12 segundos.
- Con alta frecuencia, en la cual el tiempo de pausa disminuye a 5 segundos.
La duración de cada singular impulso es de 100 milisegundos y, normalmente, cada manga recibe de 2,77 a 6,66 ciclos de limpieza cada hora, en función del intervalo de tiempo establecido entre un ciclo y otro (12 ò 5 segundos, respectivamente). En caso necesario (DP del singular compartimento es elevada y no disminuye), el operador puede establecer manualmente, tramite contraseña, una frecuencia de limpieza más alta hasta un máximo de 3,11 segundos de pausa entre un ciclo y otro. Las secuencias sobre los 4 compartimentos del filtro se desarrollan independientemente entre ellos, en base a la presión diferencial del respectivo compartimento, iniciando del lado de entrada de gases y excitando las primeras 8 electroválvulas de los primeros 8 tanques de aire (entendiendo como los primeros 2 de cada compartimento en el sentido perpendicular del flujo de gases). Después del tiempo de pausa establecido, serán excitadas las primeras 8 electroválvulas de los segundos 8 tanques, y así sucesivamente; terminados los 12 x 4 tanques de los compartimentos, el ciclo reparte con las segundas 8 electroválvulas de los primeros 8 tanques y así sucesivamente. En la Fig. 5 se muestra un detalle del compartimento D, con las electroválvulas y los tanques de aire.
4.2.3. Sistemas de protección: alta T° y DP
El filtro de mangas en cada uno de los dos conductos de ingreso de distribución de gases a los compartimentos se instala un sistema de protección contra la altísima temperatura del gas, causada por transitorios en caldera. Dicho sistema está compuesto por un ventilador y tres válvulas tipo "poppets" de comando neumático.
Una vez que llegamos a 180°C el sistema genera una señal de alarma de altísima T° e inicia a abrir automáticamente la primera válvula poppets, transcurridos un tiempo (30 s) y si la T° media no ha bajado, vendrá abierta la segunda válvula y así hasta llegar a abrir las tres al 100% para inyectar lo que se denomina "aire falso" para refrigerar el compartimento. En el caso que no sea suficiente, y la temperatura de los gases llegue al valor de 200°C, se produce el disparo de la semisección con indisponibilidad de la misma, con cierre inmediato de las compuertas de ingreso y salida de los compartimentos de dicha semisección, con el fin de proteger las mangas de cualquier posibilidad de daño y apertura automática de las compuertas de by-pass.
Al igual que para la temperatura, se instalan 3 presostatos diferenciales para la revelación de la perdida de carga aguas arriba/debajo de cada compartimento del filtro, de modo que si se alcanza el valor de alarma de 25 mbar, el operador podrá actuar de modo manual (ya que el fenómeno del aumento de presión diferencial es lento) abriendo las compuertas de equilibrio de ingreso y salida. Si continua y se llega a un valor DP=30 mbar, se produce el disparo de la semisección con indisponibilidad de la misma, con cierre inmediato de las compuertas de ingreso y salida de los compartimentos de dicha semisección, con el fin de proteger las mangas de cualquier posibilidad de daño y apertura automática de las compuertas de by-pass.
4.2.4. Sistemas de protección: alta T° y DP
El sistema de ventilación "walk in plenum" se compone de 4 ventiladores (uno por compartimento) y es el que permite realizar intervenciones de mantenimientos (sustitución de mangas) en un compartimento excluido con el filtro de mangas en servicio, manteniendo una atmósfera transitable.
Una vez interceptado el paso de gases en el compartimento con el cierre de las compuertas de ingreso y salida, se abren las válvulas rompedoras de vacío (3 por compartimento) que equilibran la presión interna-externa, y se mete en servicio en ventilador dedicado al correspondiente compartimento en mantenimiento y se abre la compuerta neumática dedicada al walk in plenum de dicho compartimento.
4.2.5. Recubrimiento de las mangas
El correcto funcionamiento de un filtro de mangas requiere respetar algunas recomendaciones, en particular en las fases de paradas y arranques de la unidad. En caso contrario es posible un daño irreversible en las mangas, con una rápida reducción de las prestaciones del filtro en términos de mayores pérdidas de carga y emisiones. En particular se debe evitar:
- En el arranque de la unidad, las partículas finas de gasoil/fuel penetran al interno de la tela de las mangas, determinando así un saturación irreversible de la misma.
- Formación de condensados en contacto directo con las mangas, puesto que pueden cementar las cenizas sobre la tela y, si es de naturaleza ácida, atacar químicamente la misma fibra.
Durante el funcionamiento normal del filtro, es la costra de cenizas que se forma sobre las mangas la que realiza la función filtrante y de protección de la tela de la formación de condensados, absorbiéndolos. Durante la fase de arranque de la unidad, en la cual no hay cenizas, el estrato de protección debe ser creado artificialmente usando productos de adecuada basicidad y granulometría. Esta operación es la que se conoce como "precoating" (recubrimiento). En el filtro se ha instalado un sistema de precoating de las mangas, utilizando normalmente calcio hidratado, aunque también es posible el uso de cenizas almacenadas.
En el caso de una parada breve de la unidad (48-72 horas), es posible evitar el precoating al arrancar con la condición de mantener el estrato de cenizas sobre las mangas y evitar la formación de condensados, por tanto se debe:
- Parar el sistema de limpieza de las mangas cuando se pare el grupo, para evitar el desprendimiento de las cenizas de las mangas
- Aislar los compartimentos del filtro manteniendo cerradas las compuertas de ingreso y salida de gases y manteniendo elevada la temperatura interior utilizando los calentadores de las tolvas inferiores
En el caso de paradas de larga duración (>72 horas), no se puede en ningún caso dejar el estrato de cenizas sobre las mangas. De hecho las cenizas, siendo higroscópicas, absorberían la humedad del aire hasta cementar sobre las mismas mangas. Por tanto, se debe meter en servicio el sistema de limpieza de las mangas y la evacuación de las tolvas durante unas horas, sucesivamente a la parada del grupo, con el objetivo de desprender la mayor cantidad posible de cenizas de las mangas.
La correcta secuencia del precoating, se obtiene metiendo en servicio los dos ventiladores de tiro inducido a máximo caudal, para obtener en los compartimentos una velocidad ascensional del aire óptima para el revestimiento de las mangas, minimizando las perdidas/caídas del agente químico (calcio hidratado) a las tolvas. Simultáneamente el agente es suministrado e impulsado mediante camiones autobotes que a través de un circuito isométrico, y se introduce en los conductos de ingreso de gas de cada semisección del filtro. La inyección de dicho agente se realiza hasta obtener un valor de DP~2÷3 mbar, que indica el correcto revestimiento de las mangas.
4.2.6. Recubrimiento de las mangas
A la hora de instalar el filtro de mangas, se plantea necesario realizar una estimación de la pérdida de carga total del sistema (incluidos los conductos), para establecer si los actuales ventiladores de tiro inducido (VTIs) son adecuadamente dimensionados para las nuevas condiciones de trabajo. Los datos para el dimensionamiento de los mismos son, Tabla 2:
- Asumir como dato de partida del diagrama piezomètrico de la instalación, la actual perdida del circuito: 68 mbar
- Las entradas de aire a considerar en los precalentadores de aire (lujngstrom) es el 15%@2.600.000 Nm3/h
- Las DP debidas a los conductos y a las compuertas de entrada y salida, se establecen típicamente en un rango de 51 - 67 mbar
- Las DP debidas a la placa portamangas, normalmente está establecida en un rango de 152-220 mbar durante el funcionamiento normal del filtro (todos los compartimentos en servicio), pero se debe prever que dichos valores se pueden incrementar si algún compartimento está aislado por limpieza "off-line" y/o mantenimiento
- Por tanto, la DP total del sistema del filtro de mangas, se estima en 20 mbar.
Así, se modificaron los motores de los actuales ventiladores de tiro inducido (VTI), sustituyéndolos por nuevos motores adaptados para ser accionados por Convertidores Electrónicos de Frecuencia (CEF).
4.3. Resultados
Los resultados de la unidad se analizan a través de varios tests de Rendimiento, los cuales se realizan, a los 6 meses y 18 meses, después de la fecha de puesta en marcha de la instalación.
Dichos tests se realizan de acuerdo a la normativa vigente de aplicación para la determinación de la cantidad de partículas presentes en los gases de combustión:
- UNI EN 13284 - 1 Enero 2003: Determinación de la concentración de partículas a la salida del filtro de mangas.
- UNI EN 13284 - 1 ò ASME PTC 38: Determinación de la concentración de partículas a la entrada del filtro de mangas.
Las condiciones del gas al ingreso del filtro se muestran en la Tabla 3. El parámetro fundamental a verificar, es la cantidad de partículas en los conductos de salida del walk in plenum, donde están instalados 2 instrumentos de control por cada compartimento. El dato debe ser referido a plena potencia de la instalación.
Tras los tests se obtuvo una máxima concentración de partículas a la salida del filtro a mangas, con todos los compartimentos en servicio de 20 mg/Nm3 (gas seco@6% O2) de concentración de media horaria, cumpliéndose así las expectativas esperadas.
5. Conclusiones y Recomendaciones
En este trabajo se han mostrado los principales problemas que afectan al funcionamiento de los precipitadores electrostáticos en las grandes instalaciones de combustión, que sumado a los límites de emisión más restrictivos hacen que la transformación a un filtro de mangas pulse-jet, aprovechando la estructura existente sea una opción particularmente interesante a considerar a la hora de afrontar importantes inversiones de mejora o sustitución de los precipitadores existentes, ya que se adaptan al espacio disponible, evitando costosos reemplazos completos, y alcanzando mayores rendimientos de captación de partículas.
Sin embargo, cada caso es diferente y va estudiado en detalle ya que depende de las condiciones específicas de cada instalación. Por ello, queremos realizar una serie de recomendaciones, deducidas de la aplicación presentada en este artículo y que deberían tenerse en cuenta para eliminar los factores que puedan contribuir al mal funcionamiento del equipo:
- El tiempo de instalación requerido varía entre 12-14 semanas. Por tanto, la viabilidad económica del proyecto sólo se puede justificar si la construcción del filtro de mangas se combina en una típica revisión general de turbina o caldera de la unidad de producción. En este caso es fundamental durante la fase de diseño maximizar en el ensamblaje de componentes y realizar un detallado programa de demolición y montaje.
- Debe existir suficiente área en planta, para adaptar el espacio requerido por las mangas. En este caso es fundamental un valor elevado de la velocidad de filtrado A/T, reduciendo las modificaciones estructurales, a la construcción de los compartimentos.
- Realizar un estudio fluido-dinámico durante la fase de diseño que permita conocer la velocidad del gas y la distribución de partículas en el interior de los compartimentos, para establecer los deflectores y desviadores adecuados de modo que el flujo sea uniforme, y alargue la vida de las mangas (3-4 años). Además, dicho estudio nos permitirá estimar las nuevas pérdidas de carga introducidas, para decidir si podemos conservar los ventiladores inducidos existentes.
Referencias
[1] Baños, R., Manzano-Agugliaro, F., Montoya, F.G., Gil, C., Alcayde, A. and Gómez, J., Optimization methods applied to renewable and sustainable energy: A review. Renewable and Sustainable Energy Reviews, 15(4), pp. 1753-1766, 2011. DOI: 10.1016/J.RSER.2010.12.008
[2] Fernández-García, A., Rojas, E., Pérez, M., Silva, R., Hernández-Escobedo, Q. and Manzano-Agugliaro, F., A parabolic-trough collector for cleaner industrial process heat. Journal of Cleaner Production, 89, pp. 272-285, 2015. DOI: 10.1016/ j.jclepro.2014.11.018
[3] Gallego-Vega, L.E. and Duarte-Velasco, O.G., The effect of electric transmission constraints on how power generation companies bid in the Colombian electrical power market. Ingeniería e Investigación, [Online]. 30(2), pp. 62-77. 2010. Available at: http://www.scielo.org.co/scielo.php?script=sci_arttext&pid=S0120-56092010000200007&lng=en&nrm=iso. ISSN 0120-5609.
[4] Manzano-Agugliaro, F. and Carrillo-Valle, J., Location of air in-leakage in power plants condensers by helium test. DYNA, 86(2), pp. pp. 173-181, 2011. DOI: 10.6036/3916
[5] Maioli, A., Pulfer, J. and Mitjans, F., Generating electricity during peak hours in Asuncion, Paraguay, through anaerobic digestion of cultivated water hyacinths. Ingeniería e Investigación, [Online]. 31, pp. 66-70, 2011 Available at: http://www.scielo.org.co/scielo.php?script=sci_arttext&pid=S0120-56092011000500010&lng=en&nrm=iso. ISSN 0120-5609.
[6] Montoya, F.G., Aguilera, M.J. and Manzano-Agugliaro, F., Renewable energy production in Spain: A review. Renewable and Sustainable Energy Reviews, 33, pp. 509-531, 2014. DOI: 10.1016/j.rser.2014.01.091
[7] de Miera, G.S., del Río-González, P. and Vizcaíno, I., Analysing the impact of renewable electricity support schemes on power prices: The case of wind electricity in Spain. Energy Policy, 36(9), pp 3345-3359, 2008. DOI: 10.1016/j.enpol.2008.04.022
[8] Wen, T.-Y., Wang, H.-C., Krichtafovitch, I. and Mamishev, A.V., Novel electrodes of an electrostatic precipitator for air filtration. Journal of Electrostatics, 73, pp. 117-124, 2015. https://doi.org /10.1016/j.elstat.2014.11.002
[9] Gutiérrez-Ortiz, F.J., Navarrete, B. and Cañadas, L., Assessment of plate-wire electrostatic precipitators based on dimensional and similarity analyses. Fuel, 90(9), pp. 2827-2835, 2011. DOI: 10.1016/j.fuel.2011.04.006
[10] Gutiérrez-Ortiz, F.J., Navarrete, B. and Cañadas, L., Dimensional analysis for assessing the performance of electrostatic precipitators. Fuel Processing Technology, 91(12), pp. 1783-1793, 2010. DOI: 10.1016/j.fuproc.2010.07.013
[11] Yan, C., Liu, G. and Chen, H., Effect of induced airflow on the surface static pressure of pleated fabric filter cartridges during pulse jet cleaning. Powder Technology, 249, pp. 424-430, 2013. DOI: 10.1016/j.powtec.2013.09.017
[12] Dang, X.-Q., Pang, M., Li, X., Zhang, J and Li, Q., Discussion on influencing factors of the pulse-jet performance of fabric filter. 2011 International Conference on Electric Technology and Civil Engineering, ICETCE 2011 - Proceedings, art. 5776073, pp. 1167-1170, 2011. DOI: 10.1109/ICETCE.2011.5776073
[13] Ait-Said, H., Nouri, H. and Zebboudj, Y., Effect of air flow on corona discharge in wire-to-plate electrostatic precipitator. Journal of Electrostatics, 73, pp. 19-25, 2015. DOI: j.elstat.2014.10.004
[14] Jdrusik, M., Gajewski, J.B. and Wierczok, A.J., Effect of the particle diameter and corona electrode geometry on the particle migration velocity in electrostatic precipitators. Journal of Electrostatics, 51-52 (1-4), pp. 245-251, 2001. DOI: S0304-3886(01)00047-X
[15] Vélez, F., Chejne, F. and Quijano, A., Thermodynamic analysis of R134a in an Organic Rankine Cycle for power generation from low temperature sources. DYNA, 81(185), pp. 153-159, 2014. DOI: 10.15446/dyna.v81n185.37598
[16] Vélez, F., Selecting working fluids in an organic Rankine cycle for power generation from low temperature heat sources. DYNA, 81(188), pp. 173-180, 2014. DOI: 10.15446/dyna.v81n188.41666
[17] Directiva de Grandes Instalaciones de Combustión (GICs) 2001/80/CE, 2001.
[18] Directiva de Emisiones Industriales (DEI) 2010/75/UE, 2010.
[19] Pavlish, J.H., Sondreal, E.A., Mann, M.D., Olson, E.S., Galbreath, K.C., Laudal, D.L. and Benson, S.A., Status review of mercury control options for coal-fired power plants. Fuel Processing Technology, 82(2-3), pp. 89-165, 2003. DOI: 10.1016/S0378-3820(03)00059-6
[20] Wara, M., Is the global carbon market working? Nature, 445 (7128), pp. 595-596, 2007. DOI: 10.1038/445595a
[21] Córdoba, P., Status of Flue Gas Desulphurisation (FGD) systems from coal-fired power plants: Overview of the physic-chemical control processes of wet limestone FGDs. Fuel, 144, pp. 274-286, 2015. DOI: 10.1016/j.fuel.2014.12.065
[22] Song, K., Jang, Y.-N., Kim, W., Lee, M.G., Shin, D., Bang, J.-H., Jeon, C.W.and Chae, S.C., Factors affecting the precipitation of pure calcium carbonate during the direct aqueous carbonation of flue gas desulfurization gypsum. Energy, 65, pp. 527-532, 2014. DOI: 10.1016/j.energy.2013.11.008
F. Manzano-Agugliaro, Obtuvo su título de Dr. Ingeniero en 1995, por la Universidad de Córdoba, España. Es profesor de la Escuela Superior de Ingeniería de Universidad de Almería, España, desde 1996, Profesor Titular de Universidad del departamento de Ingeniería desde 2001, y desde 2011 está acreditado como catedrático de Universidad por la Rama de Ingeniería y Arquitectura. Su investigación está centrada en torno a la energía, el medio ambiente, y la geomática. ORCID: 0000-0002-0085-030X
J. Carrillo-Valle, es Ing. Industrial por la Universidad de Málaga, España. En 2006 obtuvo el MSc. en "Tecnologías de Generación de Energía Eléctrica" por la Escuela Técnica Superior de Ingeniería Industrial de la Universidad Politécnica de Madrid, España. Actualmente realiza estudios en el programa de doctorado de Ingeniería Ambiental por la Universidad de Almería, España. Ha trabajado en empresas del sector energético, principalmente en el mantenimiento y operación de centrales térmicas de carbón, en diversos países como España, Italia o Chile. ORCID: 0000-0003-2406-9427
Cómo citar
IEEE
ACM
ACS
APA
ABNT
Chicago
Harvard
MLA
Turabian
Vancouver
Descargar cita
CrossRef Cited-by
1. Carmen de la Cruz-Lovera, Francisco Manzano-Agugliaro, Esther Salmerón-Manzano, José-Luis de la Cruz-Fernández, Alberto-Jesus Perea-Moreno. (2019). Date Seeds (Phoenix dactylifera L.) Valorization for Boilers in the Mediterranean Climate. Sustainability, 11(3), p.711. https://doi.org/10.3390/su11030711.
2. Miguel-Angel Perea-Moreno, Francisco Manzano-Agugliaro, Quetzalcoatl Hernandez-Escobedo, Alberto-Jesus Perea-Moreno. (2020). Sustainable Thermal Energy Generation at Universities by Using Loquat Seeds as Biofuel. Sustainability, 12(5), p.2093. https://doi.org/10.3390/su12052093.
Dimensions
PlumX
Visitas a la página del resumen del artículo
Descargas
Licencia
Derechos de autor 2016 DYNA

Esta obra está bajo una licencia internacional Creative Commons Atribución-NoComercial-SinDerivadas 4.0.
El autor o autores de un artículo aceptado para publicación en cualquiera de las revistas editadas por la facultad de Minas cederán la totalidad de los derechos patrimoniales a la Universidad Nacional de Colombia de manera gratuita, dentro de los cuáles se incluyen: el derecho a editar, publicar, reproducir y distribuir tanto en medios impresos como digitales, además de incluir en artículo en índices internacionales y/o bases de datos, de igual manera, se faculta a la editorial para utilizar las imágenes, tablas y/o cualquier material gráfico presentado en el artículo para el diseño de carátulas o posters de la misma revista.